Oxidation-extraction technology for production of hydrogen peroxide by anthraquinone process
A technology of hydrogen peroxide and anthraquinone method, applied in the directions of peroxide/peroxyhydrate/peroxyacid/superoxide/ozone, inorganic chemistry, chemical instruments and methods, etc., which can solve the problem of wall thickness and pressure level equipment There are no significant advantages in investment, low reaction rate in the oxidation process, and reduced oxidation yield, etc., to achieve the effect of improving oxidation reaction rate and extraction efficiency, improving oxidation rate and extraction efficiency, and improving oxidation yield
- Summary
- Abstract
- Description
- Claims
- Application Information
AI Technical Summary
Problems solved by technology
Method used
Image
Examples
Embodiment 1
[0032] Set up an oxidation-extraction reactor, the hydrogenation liquid and air are introduced from the bottom of the reactor, the extractant (pure water) is introduced through the middle and upper part, and after gas-liquid reaction-extraction separation-gas-liquid separation, the working liquid at the top enters the working liquid / In the hydrogen peroxide separator, the hydrogen peroxide at the bottom enters the hydrogen peroxide / working fluid separator. The oxidation-extraction reactor has a diameter of 300mm, a height of 2400mm, and a total volume of 0.17m 3 . Working fluid / hydrogen peroxide separator has a diameter of 150mm and a length of 450mm. The hydrogen peroxide / working fluid separator has a diameter of 50mm and a length of 150mm. The gas-liquid separator on the upper part of the oxidation-extraction reactor is a cyclone separation component structure. The flow rate of hydrogenated liquid is 0.29m 3 / h, the amount of air added 12Nm 3 / h, the amount of pure wat...
Embodiment 2
[0034] Set up two oxidation-extraction reactors, first introduce all the hydrogenated liquid and part of the air into the bottom of the primary oxidation-extraction reactor, the two will undergo co-current oxidation reaction from bottom to top in the reactor, and the middle and upper part will introduce secondary oxidation - The extraction agent from the extraction reactor, after oxidation reaction-extraction separation-gas-liquid separation, the hydrogenated liquid (oxidized liquid) separated in the middle and upper part is introduced into the bottom of the secondary oxidation-extraction reactor, the gas phase separated from the top and the bottom The separated hydrogen peroxide is led out of the device respectively; in the secondary oxidation-extraction reactor, the extractant (pure water) is introduced into the upper part, and the hydrogen produced in the secondary oxidation-extraction reactor is 2 o 2 It is extracted gradually, and enters the top of the primary oxidation-e...
Embodiment 3
[0036] In the three-stage oxidation / extraction reactor, all the hydrogenated liquid and part of the air are first introduced into the bottom of the primary oxidation-extraction reactor, and the two are co-currently oxidized from bottom to top in the reactor, and the middle and upper part are introduced into the secondary oxidation / extraction reactor. The extraction agent from the extraction reactor, after oxidation reaction-extraction separation-gas-liquid separation, the hydrogenated liquid (oxidized liquid) separated in the middle and upper part is introduced into the bottom of the secondary oxidation-extraction reactor, and the gas phase separated from the top is separated from the bottom The outgoing hydrogen peroxide is drawn out of the device respectively; in the secondary oxidation-extraction reactor, the extraction agent from the third-stage oxidation-extraction reactor is introduced into the middle and upper part, and at the same time, part of the oxygen-containing gas ...
PUM
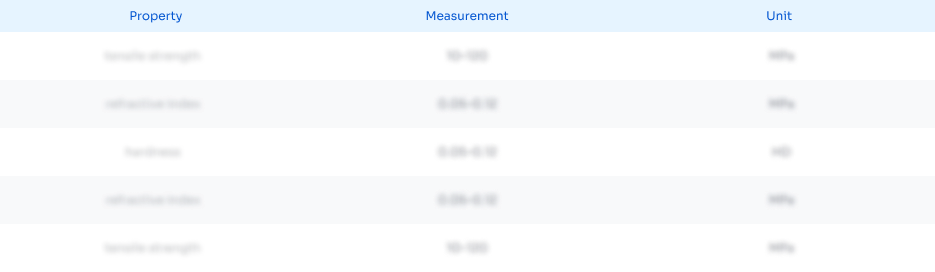
Abstract
Description
Claims
Application Information

- R&D Engineer
- R&D Manager
- IP Professional
- Industry Leading Data Capabilities
- Powerful AI technology
- Patent DNA Extraction
Browse by: Latest US Patents, China's latest patents, Technical Efficacy Thesaurus, Application Domain, Technology Topic, Popular Technical Reports.
© 2024 PatSnap. All rights reserved.Legal|Privacy policy|Modern Slavery Act Transparency Statement|Sitemap|About US| Contact US: help@patsnap.com