Manufacturing method of solid-state plasma diode for preparing holographic antenna
A manufacturing method, holographic antenna technology, applied in semiconductor/solid-state device manufacturing, antenna, antenna parts, etc., to achieve good device performance
- Summary
- Abstract
- Description
- Claims
- Application Information
AI Technical Summary
Problems solved by technology
Method used
Image
Examples
Embodiment 1
[0057] See image 3 , image 3 It is a flowchart of a method for manufacturing a solid-state plasma diode for preparing a holographic antenna according to an embodiment of the present invention. The method is suitable for preparing a lateral solid-state plasma diode based on SOI, and the solid-state plasma diode is mainly used for making a holographic antenna. The method comprises the steps of:
[0058] (a) select SOI substrate;
[0059] Among them, for step (a), the reason for using SOI substrate is that solid-state plasma antennas require good microwave characteristics, and solid-state plasma diodes need to have good carriers, that is, solid-state plasmas, in order to meet this requirement. capability, while silicon dioxide (SiO 2 ) can confine carriers, that is, solid-state plasma, in the top layer silicon, so SOI is preferably used as the substrate of solid-state plasma diodes.
[0060] (b) etching the SOI substrate to form trenches in the active region;
[0061] (c) ...
Embodiment 2
[0098] See Figure 4a-Figure 4r , Figure 4a-Figure 4r It is a schematic diagram of another method of manufacturing a solid-state plasma diode for preparing a holographic antenna according to an embodiment of the present invention; 2 The protective solid-state plasma diode is taken as an example to describe in detail, and the specific steps are as follows:
[0099] S10, selecting an SOI substrate.
[0100] See Figure 4a , the crystal orientation of the SOI substrate 101 is (100), in addition, the doping type of the SOI substrate 101 is p-type, and the doping concentration is 10 14 cm -3 Yes, the thickness of the top Si layer is, for example, 20 μm.
[0101] S20, depositing a layer of silicon nitride on the surface of the SOI substrate.
[0102] See Figure 4b A silicon nitride layer 201 is deposited on the SOI substrate 101 by using a chemical vapor deposition (Chemical vapor deposition, CVD for short) method.
[0103] S30, etching the SOI substrate to form trenches i...
Embodiment 3
[0137] Please refer to Figure 5 , Figure 5 It is a schematic diagram of the device structure of another solid-state plasma diode for preparing a holographic antenna according to an embodiment of the present invention. The solid state plasma diode employs the above as image 3 made by the fabrication method shown. Specifically, the solid-state plasma diode is prepared and formed on the SOI substrate 301, and the P region 303, the N region 304, and the i region laterally located between the P region 303 and the N region 304 of the solid-state plasma diode are all located on the SOI substrate. The top Si layer 302 at the bottom.
PUM
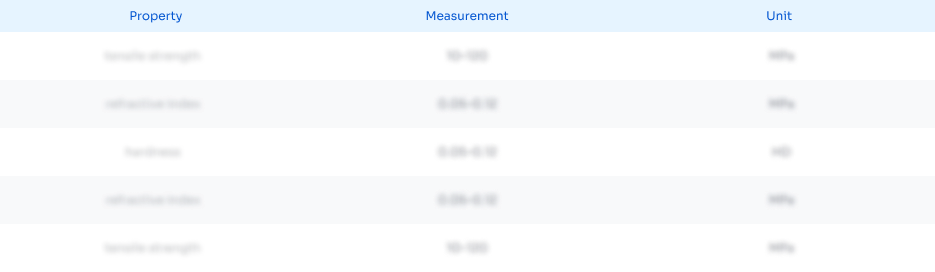
Abstract
Description
Claims
Application Information

- R&D Engineer
- R&D Manager
- IP Professional
- Industry Leading Data Capabilities
- Powerful AI technology
- Patent DNA Extraction
Browse by: Latest US Patents, China's latest patents, Technical Efficacy Thesaurus, Application Domain, Technology Topic, Popular Technical Reports.
© 2024 PatSnap. All rights reserved.Legal|Privacy policy|Modern Slavery Act Transparency Statement|Sitemap|About US| Contact US: help@patsnap.com