Probe adaptively adjusted thin-wall part on-machine ultrasonic thickness measuring method
A technology of self-adaptive adjustment and thin-walled parts, applied in the direction of using ultrasonic/sonic/infrasonic waves, measuring devices, instruments, etc., can solve the problems of large attenuation of received signals, unstable ultrasonic detection echo, and consistent normal direction, etc., to achieve Quick response, strong adaptability, and good stability
- Summary
- Abstract
- Description
- Claims
- Application Information
AI Technical Summary
Problems solved by technology
Method used
Image
Examples
specific Embodiment approach
[0022] attached figure 1 The overall appearance of the measuring device is attached. figure 2 Left sectional view of the measuring device.
[0023] The main body of the measuring device used in the embodiment is composed of an upper cover 1, a cover screw 2, a cylinder 3, a spring 4, a screw 5, a guide block 6, a lower cover 7 and a ball shaft mechanism. The specific steps of the thickness measurement method are as follows:
[0024] First, install the ball-axis mechanism as an adaptive adjustment mechanism;
[0025] The ball bushing 9 is connected to the chassis 10 through bushing screws 16, and the ball bushing 8 and the ball bushing 9 are articulated through their respective spherical contours to form a ball shaft mechanism that can realize multi-degree-of-freedom rotation. The ball shaft post 8 The other end is connected with the guide block 6 through the screw 5 to install the ultrasonic probe 11 in the chassis 10. After the surface of the ultrasonic probe 11 is adjust...
PUM
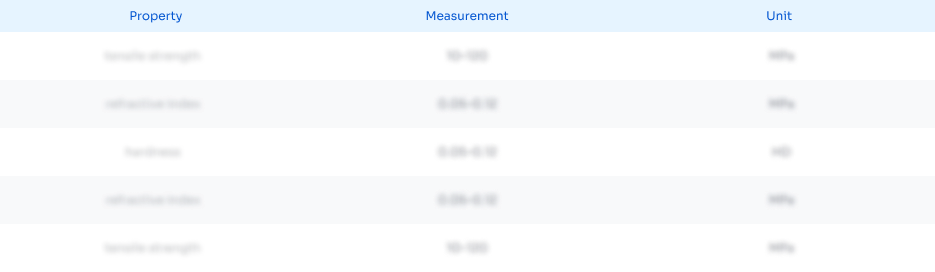
Abstract
Description
Claims
Application Information

- R&D
- Intellectual Property
- Life Sciences
- Materials
- Tech Scout
- Unparalleled Data Quality
- Higher Quality Content
- 60% Fewer Hallucinations
Browse by: Latest US Patents, China's latest patents, Technical Efficacy Thesaurus, Application Domain, Technology Topic, Popular Technical Reports.
© 2025 PatSnap. All rights reserved.Legal|Privacy policy|Modern Slavery Act Transparency Statement|Sitemap|About US| Contact US: help@patsnap.com