Binocular visual multi-line projection structured light calibration method
A binocular vision and calibration method technology, applied in image data processing, instruments, calculations, etc., can solve the problems of high precision of three-dimensional targets, increased complexity of multi-line structure cursor calibration, increased complexity, and measurement time.
- Summary
- Abstract
- Description
- Claims
- Application Information
AI Technical Summary
Problems solved by technology
Method used
Image
Examples
Embodiment
[0048] like figure 1 As shown, it is a schematic diagram of binocular vision multi-line projection structured cursor calibration. In the figure, only one structured light and two calibration board positions are drawn, as shown in figure 1 As shown, the binocular vision multi-line projection structured light system includes: a left camera 1, a right camera 2, a projector 3, a structured light plane 4, and a calibration plate 5, wherein, O l (X l ,Y l ,Z l ) is the left camera coordinate system, O r (X r ,Y r ,Z r ) is the right camera coordinate system, O g (X s ,Y g ,Z g ) is the system camera coordinate system, and point p is an intersection point between the structured smooth surface and the white line in the calibration plate; the left camera 1 and the right camera 2 are fixed on a platform to form a binocular vision system; the projector 3 is fixed In the middle of the left camera 1 and the right camera 2, so that the projected multi-line structured light is wit...
PUM
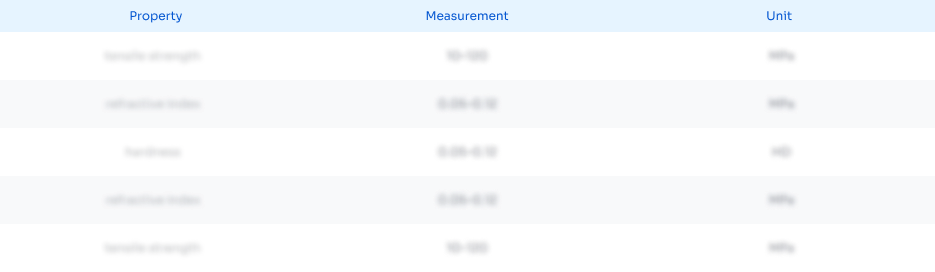
Abstract
Description
Claims
Application Information

- R&D
- Intellectual Property
- Life Sciences
- Materials
- Tech Scout
- Unparalleled Data Quality
- Higher Quality Content
- 60% Fewer Hallucinations
Browse by: Latest US Patents, China's latest patents, Technical Efficacy Thesaurus, Application Domain, Technology Topic, Popular Technical Reports.
© 2025 PatSnap. All rights reserved.Legal|Privacy policy|Modern Slavery Act Transparency Statement|Sitemap|About US| Contact US: help@patsnap.com