Self-grinding and self-rotating three-way reversing disc valve
A self-grinding, disc valve technology, applied in the direction of multi-way valves, sliding valves, valve details, etc., can solve the problems of inability to realize valve switching function, valve failure, and working condition restrictions, so as to ensure high temperature operating performance and prolong Effect of improving service life and wear performance
- Summary
- Abstract
- Description
- Claims
- Application Information
AI Technical Summary
Problems solved by technology
Method used
Image
Examples
Embodiment Construction
[0022] A self-grinding rotary three-way reversing disc valve, the structure diagram is shown in figure 1 : A closed valve cavity is formed between the upper valve body 10, the lower valve body 1 intermediate body 3 and the valve seat 9, the lower valve body 1 has an inlet, and the upper valve body 10 has a first outlet ( figure 1 The outlet on the left) and the second outlet, the angle and direction of the first outlet and the second outlet on the upper valve body 10 can be flexibly adjusted according to customer requirements, the upper and lower valve discs 4, the inlet of the lower valve body 1, the upper valve The central axes of the first outlets on the body 10 do not coincide with each other, and there is eccentricity. This unique eccentric setting ensures that the upper and lower valve discs 4 are subjected to unbalanced friction when they move, and the friction causes the valve discs 4 to rotate around their central axes. Self-rotation; the valve disc 4 is connected wit...
PUM
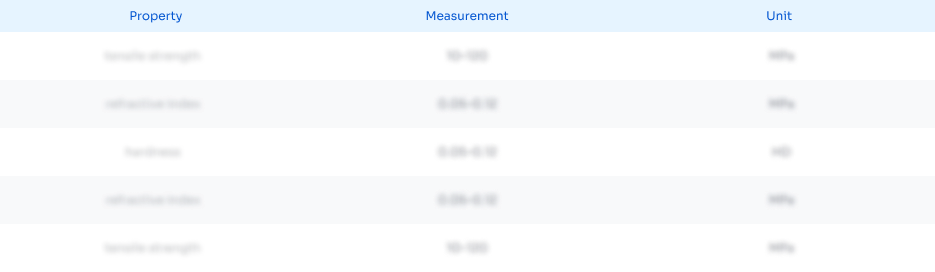
Abstract
Description
Claims
Application Information

- R&D
- Intellectual Property
- Life Sciences
- Materials
- Tech Scout
- Unparalleled Data Quality
- Higher Quality Content
- 60% Fewer Hallucinations
Browse by: Latest US Patents, China's latest patents, Technical Efficacy Thesaurus, Application Domain, Technology Topic, Popular Technical Reports.
© 2025 PatSnap. All rights reserved.Legal|Privacy policy|Modern Slavery Act Transparency Statement|Sitemap|About US| Contact US: help@patsnap.com