Melt-blown nonwoven fabric production system capable of increasing particle embedding rate
A melt-blown non-woven fabric and production system technology, applied in non-woven fabrics, textiles and papermaking, feeding solution to spinnerets, etc., can solve the problems of low embedding rate of functional nanoparticles and poor firmness, etc. The effect of increasing particle embedding rate and improving bond fastness
- Summary
- Abstract
- Description
- Claims
- Application Information
AI Technical Summary
Problems solved by technology
Method used
Image
Examples
Embodiment
[0021] The activated carbon nanoparticles are fed by the feeding device 7, and the stirring rod 7-5 in the feeding device 7 rotates under the drive of the stirring motor 7-1, and the nanoparticles are fed from the storage bin 7 under the action of the stirring rod 7-5. -11 falls into the powder falling chamber 7-7, the driving motor 7-14 drives the powder wheel 7-6 to rotate, and the nanoparticles in the powder falling chamber 7-7 are sent into the hot air pipeline 7-8, and through the air outlet 7-19 It is ejected together with the high-temperature and high-pressure airflow.
[0022] The polypropylene slices are fed by the feeding hopper 1, melted and output into the die head 4 through the screw extruder 3 driven by the system motor 2, and then sprayed into fibers through the nozzle hole of the die head 4 and passed through the hot air source connected with 7-19 The high-temperature air flow pipe in 6 enters the high-pressure hot air flow, and evenly adheres to the surface of...
PUM
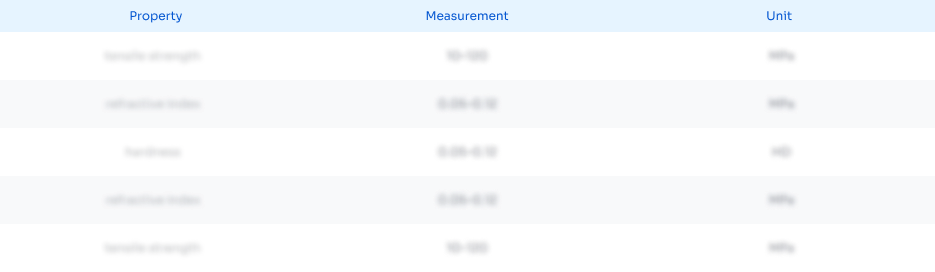
Abstract
Description
Claims
Application Information

- R&D Engineer
- R&D Manager
- IP Professional
- Industry Leading Data Capabilities
- Powerful AI technology
- Patent DNA Extraction
Browse by: Latest US Patents, China's latest patents, Technical Efficacy Thesaurus, Application Domain, Technology Topic, Popular Technical Reports.
© 2024 PatSnap. All rights reserved.Legal|Privacy policy|Modern Slavery Act Transparency Statement|Sitemap|About US| Contact US: help@patsnap.com