Method for producing cryolites by using aluminum electrolytic cell cathode carbon block alkaline leaching solution
A technology of cathode carbon block and aluminum electrolytic cell, which is applied in the direction of aluminum fluoride and aluminum halide, and can solve the problems of alkaline immersion solution pollution and shortening process of aluminum electrolytic cell cathode carbon block
- Summary
- Abstract
- Description
- Claims
- Application Information
AI Technical Summary
Problems solved by technology
Method used
Examples
Embodiment 1
[0077] Grind 100g of aluminum electrolytic cell cathode carbon block to -200 mesh and account for 75% of the total particle weight, then mix it with NaOH solution with a mass fraction of 20% according to the liquid-solid mass ratio of 6:1, and prepare the slurry at a heating temperature of 60°C. The leaching was carried out for 1.5 h under the condition of a stirring rate of 180 r / min, and the first filtrate and the first filter residue were obtained by filtering after the reaction. Add sodium fluoride to the first filtrate to adjust Al:Na:F=1:3.1:6.3, then add 1gNa 3 AlF 6 Solid, then according to the rate of 12.5L / h into the rich NH 3 Gas, to ensure that the element N:Al in the solution is 4.2:1, at 50°C and 170r / min, a precipitate is formed, react for 30min, filter to obtain the second filtrate and the second filter residue, and dry the second filter residue at 120°C to obtain cryolite product. Finally, 33.58 g of cryolite with a purity of 97.65% and a molecular ratio of...
Embodiment 2
[0087] Grind 100g of aluminum electrolytic cell cathode carbon block to -200 mesh and account for 75% of the total particle weight, then mix it with NaOH solution with a mass fraction of 20% according to the liquid-solid mass ratio of 6:1, and prepare the slurry at a heating temperature of 60°C. The leaching was carried out for 1.5 h under the condition of a stirring rate of 180 r / min, and the first filtrate and the first filter residue were obtained by filtering after the reaction. Add sodium fluoride to the first filtrate to adjust Al:Na:F=1:3.1:6.3, then add 1gNa 3 AlF 6 Solid, then according to the rate of 15L / h into the rich NH with a purity of 60% 3 Gas, to ensure that the element N:Al in the solution is 4.2:1, at 50°C and 170r / min, a precipitate is formed, react for 30min, filter to obtain the second filtrate and the second filter residue, and dry the second filter residue at 120°C to obtain cryolite product. Finally, 32.89 g of cryolite with a purity of 96.71% and a...
Embodiment 3
[0089] Grind 100g of aluminum electrolytic cell cathode carbon block to -200 mesh and account for 75% of the total particle weight, then mix it with NaOH solution with a mass fraction of 20% according to the liquid-solid mass ratio of 6:1, and prepare the slurry at a heating temperature of 60°C. The leaching was carried out for 1.5 h under the condition of a stirring rate of 180 r / min, and the first filtrate and the first filter residue were obtained by filtering after the reaction. Add sodium fluoride to the first filtrate to adjust Al:Na:F=1:3.1:6.3, then add 1gNa 3 AlF 6 solid, followed by feeding 50% pure NH at a rate of 10L / h 3 Gas, to ensure that the element N:Al in the solution is 4.2:1, at 50°C and 170r / min, a precipitate is formed, react for 30min, filter to obtain the second filtrate and the second filter residue, and dry the second filter residue at 120°C to obtain cryolite product. Finally, 33.21 g of cryolite with a purity of 97.07% and a molecular ratio of 2.9...
PUM
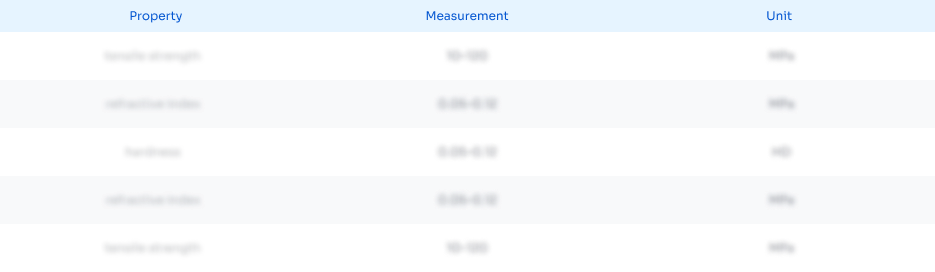
Abstract
Description
Claims
Application Information

- R&D
- Intellectual Property
- Life Sciences
- Materials
- Tech Scout
- Unparalleled Data Quality
- Higher Quality Content
- 60% Fewer Hallucinations
Browse by: Latest US Patents, China's latest patents, Technical Efficacy Thesaurus, Application Domain, Technology Topic, Popular Technical Reports.
© 2025 PatSnap. All rights reserved.Legal|Privacy policy|Modern Slavery Act Transparency Statement|Sitemap|About US| Contact US: help@patsnap.com