Aluminum alloy for heat exchanger fins
A heat exchanger, aluminum alloy technology, applied in material science, aluminum manufacturing, metallurgy, material chemistry, aluminum alloy fields, can solve problems such as small corrosion potential
- Summary
- Abstract
- Description
- Claims
- Application Information
AI Technical Summary
Problems solved by technology
Method used
Image
Examples
example 1
[0054]Will contain 1.0wt.%-1.1wt.% Si, 0.37wt.%-0.42wt.% Fe; 1.5wt.%-1.6wt.% Zn, 1.3wt.%-1.35wt.% Mn, 0.27wt.% - 0.33wt.% Cu, 0.04wt.% -0.05wt.% Mg aluminum alloy, the rest of which is aluminum and unavoidable impurities, DC casting into ingots. The ingots were preheated to 480°C at a heating rate of 50°C / hr within 12 hours, submerged at 460°C-480°C for 6 hours and hot rolled to a thickness of 3.5mm-4mm. Subsequently, the sheet was cold-rolled to a thickness of about 1 mm, and then to an intermediate thickness of about 123 μm, followed by an intermediate annealing treatment comprising soaking at 350° C. for 4 hours with 50° C. / Constant heating and cooling rates of hr, and subsequent cold rolling to a final wire diameter of about 80 μm, which corresponds to 35% CW. The resulting alloy material has a minimum ultimate tensile strength of about 220 MPa in the pre-brazing condition and about 150 MPa-160 MPa after brazing. The alloy material has an average electrical conductivity...
example 2
[0056] Will contain 1.0wt.%-1.1wt.% Si, 0.37wt.%-0.42wt.% Fe; 1.5wt.%-1.6wt.% Zn, 1.3wt.%-1.35wt.% Mn, 0.27wt.% - 0.33wt.% Cu, 0.04wt.% -0.05wt.% Mg aluminum alloy, the rest of which is aluminum and unavoidable impurities, DC casting into ingots. The ingots were preheated to 480°C at a heating rate of 50°C / hr within 12 hours, submerged at 460°C-480°C for 6 hours and hot rolled to a thickness of 3.5mm-4mm. Subsequently, the sheet was cold rolled to a thickness of about 1 mm, and then to an intermediate thickness, followed by an intermediate annealing treatment at two different temperatures. For intermediate annealing, alloy samples were subjected to immersion at 350°C or 500°C for 4 hours, with a constant heating and cooling rate of 50°C / hr applied before and after immersion, and subsequent cold rolling to a final wire diameter of approximately 80 μm , which corresponds to 40% CW. The alloy samples were examined for sag resistance and post-braze microstructure after applying ...
PUM
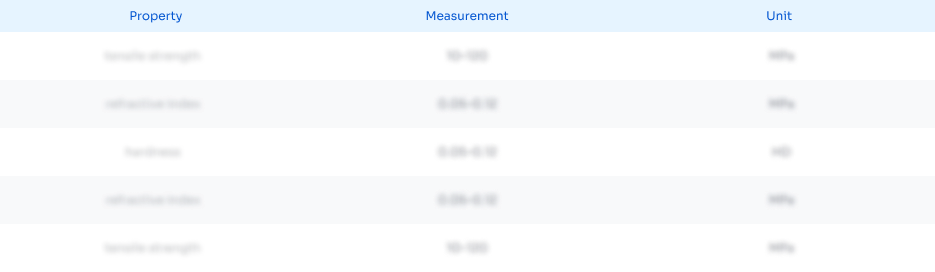
Abstract
Description
Claims
Application Information

- R&D
- Intellectual Property
- Life Sciences
- Materials
- Tech Scout
- Unparalleled Data Quality
- Higher Quality Content
- 60% Fewer Hallucinations
Browse by: Latest US Patents, China's latest patents, Technical Efficacy Thesaurus, Application Domain, Technology Topic, Popular Technical Reports.
© 2025 PatSnap. All rights reserved.Legal|Privacy policy|Modern Slavery Act Transparency Statement|Sitemap|About US| Contact US: help@patsnap.com