Polishing pad
A polishing pad and polishing layer technology, applied in the field of polishing pads, can solve the problems of decreased product yield, distribution of polishing liquid, irregular overall structure, etc., and achieve the effects of improving wafer planarization, polishing rate, and simple structure.
- Summary
- Abstract
- Description
- Claims
- Application Information
AI Technical Summary
Problems solved by technology
Method used
Image
Examples
Embodiment Construction
[0036] First, a brief description of the polishing machine, the polishing machine platen can be rotated around its axis of rotation by the platen drive. The wafer can be supported by the wafer carrier and rotated about its axis of rotation. The wafer includes a polished surface, which faces the polishing pad and is planarized during the polishing process. The wafer carrier can be supported by a carrier support assembly, which is suitable for rotating the wafer during the polishing process and provides a downward force F to press the polished surface of the wafer 4 against the polishing pad, so that the polishing surface and the polishing pad There is the required pressure between. The polishing machine is also equipped with a polishing liquid feed port for conveying polishing liquid to the polishing pad. The polishing liquid feeding port should usually be placed at or near the axis of rotation of the polishing machine platen to optimize the polishing effect of the polishing p...
PUM
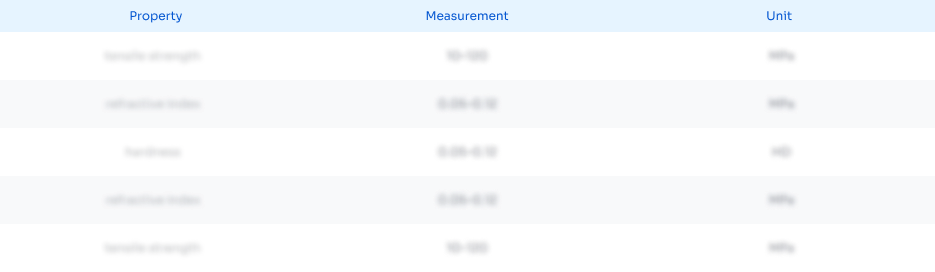
Abstract
Description
Claims
Application Information

- R&D
- Intellectual Property
- Life Sciences
- Materials
- Tech Scout
- Unparalleled Data Quality
- Higher Quality Content
- 60% Fewer Hallucinations
Browse by: Latest US Patents, China's latest patents, Technical Efficacy Thesaurus, Application Domain, Technology Topic, Popular Technical Reports.
© 2025 PatSnap. All rights reserved.Legal|Privacy policy|Modern Slavery Act Transparency Statement|Sitemap|About US| Contact US: help@patsnap.com