Hole plugging method of PCB
A technology of plug holes and front holes, which is applied in the direction of electrical connection formation of printed components, electrical components, printed circuits, etc., can solve the problems of difficulty in making outer layer circuits, reduce the uniformity of outer layer copper layer thickness, and high product defect rate, and achieve The effect of improving production capacity, reducing the number of grinding plates, and improving production efficiency
- Summary
- Abstract
- Description
- Claims
- Application Information
AI Technical Summary
Problems solved by technology
Method used
Image
Examples
Embodiment 1
[0017] This embodiment provides a method for manufacturing a PCB, in which copper paste plug holes need to be manufactured on the PCB. And in order to illustrate the technical content of the present invention, the holes on the PCB of this embodiment are designed to be plugged with copper paste, and there is no need to make other metallized holes and metallized holes filled with other materials.
[0018] The specification parameters of the prepared PCB are as follows:
[0019]
[0020] Specific steps are as follows:
[0021] (1) Multi-layer production board
[0022] According to the existing technology, the inner layer core board and the outer layer copper foil are made into a multi-layer production board through the process of material cutting → negative film making of the inner layer circuit → pressing → drilling → copper sinking → full board electroplating, that is, the inner layer core board and the outer layer copper foil are made into a multi-layer production board T...
Embodiment 2
[0054] This embodiment provides a method for manufacturing a PCB, in which copper paste plug holes need to be manufactured on the PCB. In addition to the copper paste plug holes, other metallized holes (such as metallized through holes and metallized blind holes) need to be formed on the PCB of this embodiment.
[0055] The specification parameters of the prepared PCB are as follows:
[0056]
[0057] Specific steps are as follows:
[0058] (1) Multi-layer production board
[0059] According to the existing technology, the inner layer core board and the outer layer copper foil are made into a multi-layer production board through the process of material cutting → negative film making of the inner layer circuit → pressing → drilling → copper sinking → full board electroplating, that is, the inner layer core board and the outer layer copper foil are made into a multi-layer production board The core board, the prepreg and the outer copper foil are laminated into one productio...
PUM
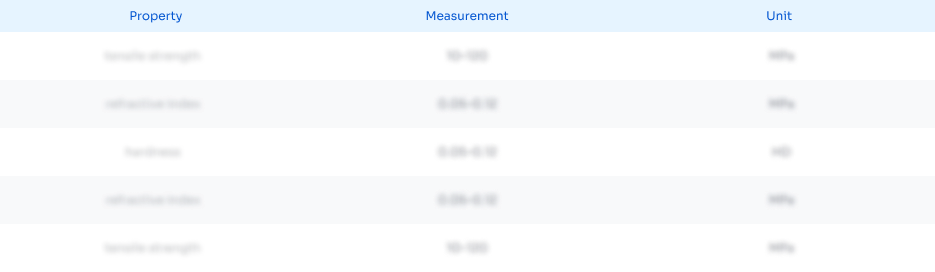
Abstract
Description
Claims
Application Information

- R&D
- Intellectual Property
- Life Sciences
- Materials
- Tech Scout
- Unparalleled Data Quality
- Higher Quality Content
- 60% Fewer Hallucinations
Browse by: Latest US Patents, China's latest patents, Technical Efficacy Thesaurus, Application Domain, Technology Topic, Popular Technical Reports.
© 2025 PatSnap. All rights reserved.Legal|Privacy policy|Modern Slavery Act Transparency Statement|Sitemap|About US| Contact US: help@patsnap.com