Treatment method for slab retention in slab continuous casting
A processing method and slab continuous casting technology, which is applied in the field of slab continuous casting stagnant slab processing, can solve problems such as increased resistance to casting, failure of driving rollers, and failure to achieve the effect of casting, so as to reduce the resistance of casting , Guaranteed pulling out, time-saving effect
- Summary
- Abstract
- Description
- Claims
- Application Information
AI Technical Summary
Problems solved by technology
Method used
Image
Examples
Embodiment 1
[0034] A slab continuous casting stagnant slab treatment method, the method is implemented according to the following steps:
[0035] First of all, determine the types and causes of stagnant billet. According to the current situation of stagnant billet that has occurred in slab continuous casting machines at home and abroad, it can be roughly divided into two categories: (1) Continuous casting caused by equipment failure and operational reasons The machine has a long downtime, and the slab is stagnant due to overcooling of the slab, or the local thickness of the slab exceeds the set value caused by the failure of the process, continuous casting cooling, and hydraulic equipment; (2) The continuous casting machine has abnormal process accidents , such as breakout and overflow of steel, resulting in cold steel jamming or stagnation caused by bonding between slabs and other equipment of the casting machine;
[0036] 1. Long downtime of continuous casting machine caused by equipmen...
PUM
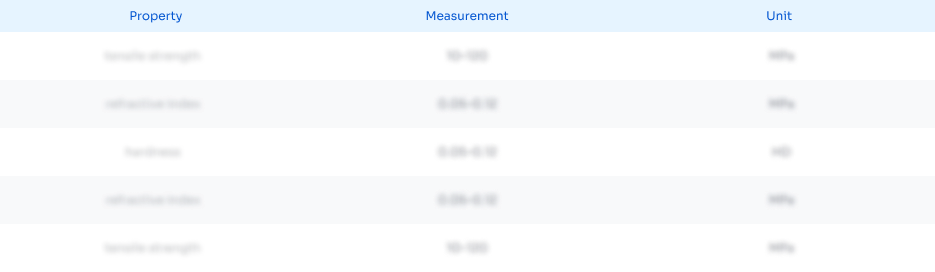
Abstract
Description
Claims
Application Information

- Generate Ideas
- Intellectual Property
- Life Sciences
- Materials
- Tech Scout
- Unparalleled Data Quality
- Higher Quality Content
- 60% Fewer Hallucinations
Browse by: Latest US Patents, China's latest patents, Technical Efficacy Thesaurus, Application Domain, Technology Topic, Popular Technical Reports.
© 2025 PatSnap. All rights reserved.Legal|Privacy policy|Modern Slavery Act Transparency Statement|Sitemap|About US| Contact US: help@patsnap.com