Manufacturing technique for honeycomb chassis thin wall
A manufacturing process and thin-walled technology, which is applied in the thin-walled manufacturing process of honeycomb chassis, can solve the problems of increased chassis size error, increased manufacturing cost, time-consuming assembly, etc., and achieve the effects of increased strength, cost saving, and reliable connection
- Summary
- Abstract
- Description
- Claims
- Application Information
AI Technical Summary
Problems solved by technology
Method used
Image
Examples
Embodiment Construction
[0018] refer to Figure 1-Figure 4 As shown, in this embodiment, a thin-walled manufacturing process of a honeycomb chassis is characterized in that the process includes the following steps:
[0019] This process adopts a die-casting process, and sixty-four hexagonal thin-walled honeycomb structures 1 can be die-casted each time.
[0020] The transition fillet 2 can increase the strength of the honeycomb chassis and meet the production process requirements during die-casting, and the entire thin-walled honeycomb structure is demoulded by the ejector pin at this fillet.
[0021] The workpiece produced by die-casting will be heavier than the mass of profile extrusion. To solve this problem, double-sided drafting is used. The drafting end point 7 is in the middle of the hexagonal thin-walled honeycomb structure, and the drafting is carried out from the upper end surface and the lower end surface to the middle part at the same time, forming a special honeycomb structure with a th...
PUM
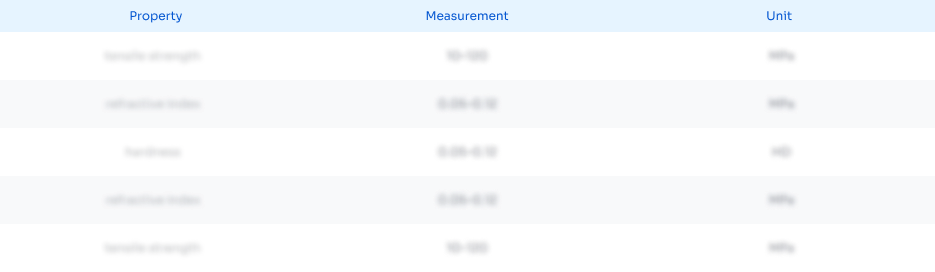
Abstract
Description
Claims
Application Information

- Generate Ideas
- Intellectual Property
- Life Sciences
- Materials
- Tech Scout
- Unparalleled Data Quality
- Higher Quality Content
- 60% Fewer Hallucinations
Browse by: Latest US Patents, China's latest patents, Technical Efficacy Thesaurus, Application Domain, Technology Topic, Popular Technical Reports.
© 2025 PatSnap. All rights reserved.Legal|Privacy policy|Modern Slavery Act Transparency Statement|Sitemap|About US| Contact US: help@patsnap.com