Hydraulic actuator and method for operating a hydraulic actuator
A technology of hydraulic actuators and piezoelectric actuators, applied in fluid pressure actuators, piezoelectric effect/electrostrictive or magnetostrictive motors, generators/motors, etc., can solve the problem of high actuators Stiffness and other issues
- Summary
- Abstract
- Description
- Claims
- Application Information
AI Technical Summary
Problems solved by technology
Method used
Image
Examples
Embodiment Construction
[0019] figure 1 The illustrated hydraulic actuator 5 according to the invention comprises a piezoelectric actuator 10 kinematically coupled to a drive piston 15 of a hydraulic drive cylinder 20 .
[0020] The drive cylinder 20 comprises a hydraulic drive volume 25 filled with hydraulic oil in a manner known per se. This drive volume 25 is hydraulically coupled to a hydraulic output cylinder 35 via a check valve 30 in order to open when a sufficiently high opening pressure exists. The non-return valve 30 is correspondingly prestressed. On the drive side, the output cylinder 35 has an output volume 40 which moves an output piston 45 on the output side.
[0021] Furthermore, the drive volume is coupled via a check valve 50 to a reservoir 55 so that the drive volume can be supplied to this reservoir.
[0022] Furthermore, the drive volume 25 can be supplied to the prestressing volume 70 of the hydraulic prestressing cylinder 90 via the nonreturn valve 60 and the throttle valve ...
PUM
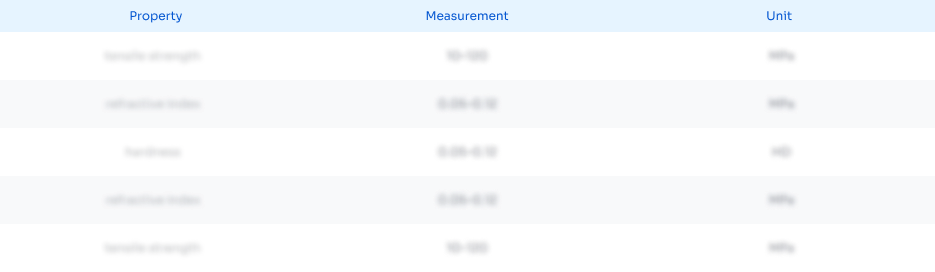
Abstract
Description
Claims
Application Information

- R&D Engineer
- R&D Manager
- IP Professional
- Industry Leading Data Capabilities
- Powerful AI technology
- Patent DNA Extraction
Browse by: Latest US Patents, China's latest patents, Technical Efficacy Thesaurus, Application Domain, Technology Topic, Popular Technical Reports.
© 2024 PatSnap. All rights reserved.Legal|Privacy policy|Modern Slavery Act Transparency Statement|Sitemap|About US| Contact US: help@patsnap.com