Preparation method of gas-generating arc-extinguishing material for high-voltage fuse
A technology of high-voltage fuses and arc-extinguishing materials, applied in electrical components, emergency protection devices, circuits, etc., can solve the problems of reduced safety factor of fuses, poor frost resistance, and size changes, and achieve reliable arc-extinguishing performance, Obvious comprehensive technical and economic effect, not easy to soften the effect
- Summary
- Abstract
- Description
- Claims
- Application Information
AI Technical Summary
Problems solved by technology
Method used
Examples
example 1
[0024]Weigh 200g of nylon 6 fiber, wrap it with gauze, immerse it in a fermenter containing 2L of biogas liquid, and ferment it at a constant temperature for 6 hours at a temperature of 30°C, then separate and remove the gauze, take out the nylon 6 fiber, and wash it with deionized water Wash 3 times, then immerse it in a beaker filled with 600mL ethanol solution with a mass fraction of 70%, and then transfer the beaker to an ultrasonic oscillator, under the condition of 200W power, sonicate for 15min, filter, collect nylon 6 fibers, and It was transferred to an oven, dried at 75°C for 2 hours, and then cut into nylon staple fibers with a length of 6 mm; in a three-necked flask filled with 60 mL of anhydrous tetrahydrofuran, 0.6 g of potassium tert-butoxide, 0.3 g of bicyclic Hexyl-18-crown ether-6, 10g of the nylon staple fiber obtained above, and then pass nitrogen gas into the three-necked flask at a rate of 3mL / min until all the air is replaced, and then place the flask in ...
example 2
[0027] Weigh 260g of nylon 6 fiber, wrap it with gauze, immerse it in a fermenter containing 3L of biogas liquid, and ferment it at a constant temperature for 7 hours at a temperature of 32°C, then separate and remove the gauze, take out the nylon 6 fiber, and wash it with deionized water Wash 4 times, then immerse it in a beaker filled with 700mL ethanol solution with a mass fraction of 72%, and then transfer the beaker to an ultrasonic oscillator, under the condition of 250W power, ultrasonic 18min, filter, collect nylon 6 fiber, and It was transferred to an oven, dried at 78°C for 3 hours, and then cut into nylon staple fibers with a length of 7 mm; in a three-necked flask filled with 65 mL of anhydrous tetrahydrofuran, 0.7 g of potassium tert-butoxide, 0.4 g of bicyclic Hexyl-18-crown ether-6, 12g of the nylon staple fiber obtained above, and then pass nitrogen gas into the three-necked flask at a rate of 4mL / min until all the air is replaced, and then place the flask in a ...
example 3
[0030] Weigh 300g of nylon 6 fiber, wrap it with gauze, immerse it in a fermenter containing 4L of biogas liquid, and ferment it at a constant temperature for 8 hours at a temperature of 35°C, then separate and remove the gauze, take out the nylon 6 fiber, and wash it with deionized water Wash 5 times, then immerse it in a beaker filled with 800mL of ethanol solution with a mass fraction of 75%, and then transfer the beaker to an ultrasonic oscillator. Under the condition of 300W power, ultrasonic for 20min, filter, collect nylon 6 fiber, and It was transferred to an oven, dried at 80°C for 4 hours, and then cut into 8 mm long nylon staple fibers; in a three-necked flask filled with 75 mL of anhydrous tetrahydrofuran, 0.8 g of potassium tert-butoxide, 0.5 g of bicyclic Hexyl-18-crown ether-6, 15g of the nylon staple fiber obtained above, and then pass nitrogen into the three-necked flask at a rate of 5mL / min until all the air is replaced, and then place the flask in a digital s...
PUM
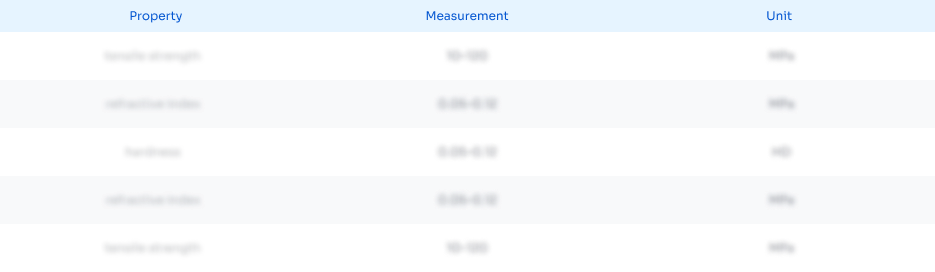
Abstract
Description
Claims
Application Information

- Generate Ideas
- Intellectual Property
- Life Sciences
- Materials
- Tech Scout
- Unparalleled Data Quality
- Higher Quality Content
- 60% Fewer Hallucinations
Browse by: Latest US Patents, China's latest patents, Technical Efficacy Thesaurus, Application Domain, Technology Topic, Popular Technical Reports.
© 2025 PatSnap. All rights reserved.Legal|Privacy policy|Modern Slavery Act Transparency Statement|Sitemap|About US| Contact US: help@patsnap.com