A method for improving the recovery rate of iron components in steel slag
A recovery rate, steel slag technology, applied in the direction of recycling technology, chemical instruments and methods, solid separation, etc., can solve the problems of oxidative gas oxidation degree control, inconvenient on-site operation, etc., to achieve the benefits of secondary utilization, heavy metal reduction, The effect of improving the recovery rate
- Summary
- Abstract
- Description
- Claims
- Application Information
AI Technical Summary
Problems solved by technology
Method used
Examples
no. 1 example
[0046] Add 16% (mass percentage) river sand into the molten electric furnace slag, and the silicon oxide content of the river sand is 71.26%; further air-cool the evenly melted modified slag, and break some samples of the modified electric furnace slag after cooling Ball mill to below 200 mesh for magnetic separation. The test results showed that the basicity of the modified steel slag was reduced from 2.35 to 1.42, Fe 2 o 3 The ratio to the FeO content (mass percentage) is 0.81, and the recovery rate of the iron component is 60.47%.
[0047] The unmodified steel slag is recovered by conventional methods, and the recovery rate is 31.75%. The iron component is recovered after the steel slag is modified by the method, and the recovery rate of the steel slag without modification is increased by 90.40%. The ferromagnetic mineral phase of the iron component recovered in this embodiment is mainly magnetite and iron-containing spinel.
no. 2 example
[0049] Add 20% (mass percentage) iron tailings in the molten electric furnace slag, and the SiO2+Fe2O3 content of the iron tailings is 79.90%; further air-cool the modified molten slag, and after cooling, the modified electric furnace slag Part of the samples were crushed and ball milled to below 200 mesh for magnetic separation. The test results show that the basicity of modified steel slag is reduced from 2.35 to 1.38, the ratio of Fe2O3 to FeO content (mass percentage) is 0.99, and the iron recovery rate is 73.71%, which is 132.09% higher than that of unmodified steel slag.
no. 3 example
[0051] Add 25% (mass percentage) river sand into the molten converter slag, and the silicon oxide content of the river sand is 71.26%; further air-cool the evenly melted modified slag, and break some samples of the modified converter slag after cooling Ball mill to below 200 mesh for magnetic separation. The test results showed that the basicity of the modified steel slag was reduced from 2.35 to 1.39, Fe 2 o 3 The ratio of FeO content (mass percentage) is 1.88, and the recovery rate of iron is 50.59%, which is 59.29% higher than that of unmodified steel slag.
PUM
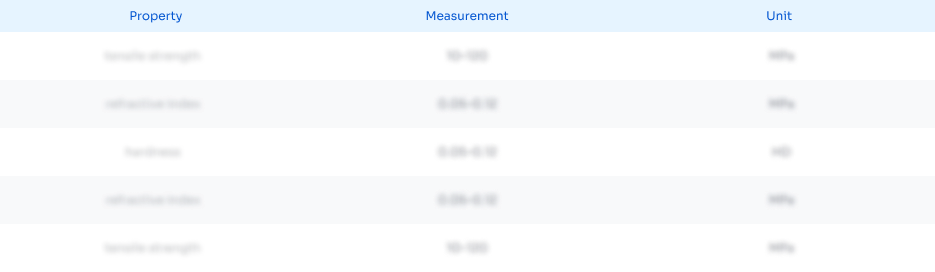
Abstract
Description
Claims
Application Information

- Generate Ideas
- Intellectual Property
- Life Sciences
- Materials
- Tech Scout
- Unparalleled Data Quality
- Higher Quality Content
- 60% Fewer Hallucinations
Browse by: Latest US Patents, China's latest patents, Technical Efficacy Thesaurus, Application Domain, Technology Topic, Popular Technical Reports.
© 2025 PatSnap. All rights reserved.Legal|Privacy policy|Modern Slavery Act Transparency Statement|Sitemap|About US| Contact US: help@patsnap.com