Fresh air heating and humidifying and exhaust gas impurity removal integrated method
A technology for fresh air and fresh air passages, applied in chemical instruments and methods, separation methods, dry gas layout, etc., can solve the problems of easy blockage of heat exchangers by large particles of impurities, unsuitable heat recovery, and low heat recovery rate. The effect is not good, the temperature rise is reduced, and the heat exchange area is large.
- Summary
- Abstract
- Description
- Claims
- Application Information
AI Technical Summary
Problems solved by technology
Method used
Image
Examples
Embodiment Construction
[0033] In order for those skilled in the art to better understand the technical solution of the present invention, the present invention will be further described below in conjunction with the examples and accompanying drawings, but the embodiments of the present invention are not limited thereto.
[0034] see Figure 1-3 , the integrated method of fresh air heating, humidification and exhaust impurity removal in this embodiment includes the following steps:
[0035] The exhaust gas is passed into the impurity removal chamber 1, and the exhaust gas is blown from the exhaust inlet 1-1 of the impurity removal chamber 1 to the impurity removal wall 2 provided with a fresh air passage 3 inside.
[0036] The miscellaneous removal wall 2 restricts the flow space and flow direction of the exhaust gas, reduces the flow velocity of the exhaust gas, and the impurities settle down under the action of gravity; at the same time, the exhaust gas is in contact with the miscellaneous removal ...
PUM
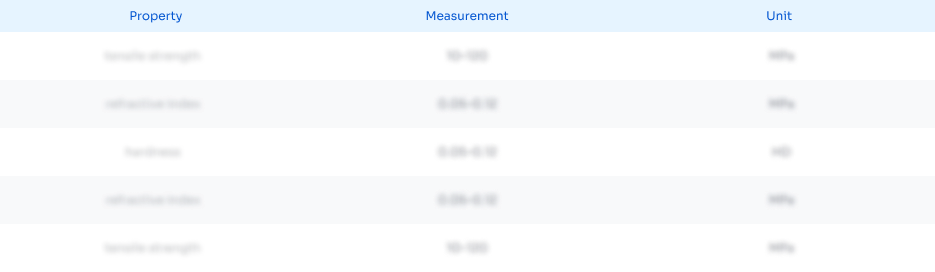
Abstract
Description
Claims
Application Information

- R&D Engineer
- R&D Manager
- IP Professional
- Industry Leading Data Capabilities
- Powerful AI technology
- Patent DNA Extraction
Browse by: Latest US Patents, China's latest patents, Technical Efficacy Thesaurus, Application Domain, Technology Topic, Popular Technical Reports.
© 2024 PatSnap. All rights reserved.Legal|Privacy policy|Modern Slavery Act Transparency Statement|Sitemap|About US| Contact US: help@patsnap.com