Rear floor assembly reversing tooling vehicle
A technology for turning over the assembly and the rear floor, which is applied to the direction of the workbench, auxiliary devices, manufacturing tools, etc., can solve the problems of poor control of manual turning force, poor turning stability, bump damage of the rear floor assembly, etc., to achieve convenient and stable laying The effect of solder joint or solder joint quality inspection
- Summary
- Abstract
- Description
- Claims
- Application Information
AI Technical Summary
Problems solved by technology
Method used
Image
Examples
Embodiment Construction
[0014] Referring to the drawings, a rear floor assembly turning tooling vehicle includes a chassis 10 and a bracket 20 mounted on the chassis 10. The bracket 20 includes a first and a second parallel standing at the front and rear ends of the chassis 10 Two supporting rods 21, 22, the top ends of the first and second supporting rods 21, 22 are symmetrically provided with first and second bearing seats 23, 24, and the first bearing seat 23 is provided with a first rotating shaft 25, The first rotating shaft 25 is located on the inner side of the first bearing seat 23 and is fixedly connected with a first limiting plate 30. On the first limiting plate 30, two block pins 31 are symmetrically provided with the first rotating shaft 25 as a symmetrical axis. A first support plate 32 is symmetrically provided on the position plate 30 below the block pin 31, a second rotation shaft 26 is provided on the second bearing seat 24, and the second rotation shaft 26 is located inside the secon...
PUM
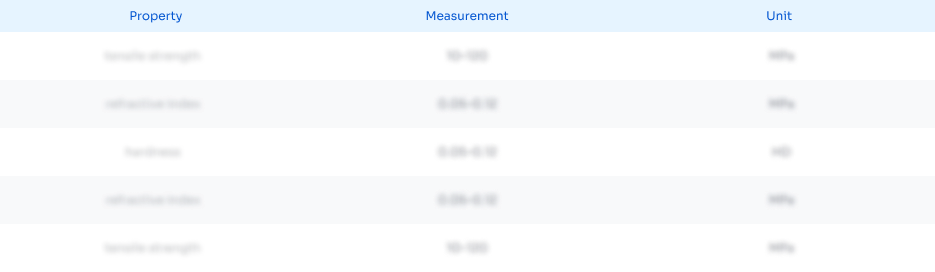
Abstract
Description
Claims
Application Information

- R&D
- Intellectual Property
- Life Sciences
- Materials
- Tech Scout
- Unparalleled Data Quality
- Higher Quality Content
- 60% Fewer Hallucinations
Browse by: Latest US Patents, China's latest patents, Technical Efficacy Thesaurus, Application Domain, Technology Topic, Popular Technical Reports.
© 2025 PatSnap. All rights reserved.Legal|Privacy policy|Modern Slavery Act Transparency Statement|Sitemap|About US| Contact US: help@patsnap.com