Fabricated type cavity board for forming bidirectional-loading floor system
A cavity board, assembled technology, applied in the direction of floor slabs, building components, buildings, etc., can solve the problems of long molding time, difficult industrial production, poor integrity of the filling body and easy damage, etc.
- Summary
- Abstract
- Description
- Claims
- Application Information
AI Technical Summary
Problems solved by technology
Method used
Image
Examples
Embodiment Construction
[0026] The invention will be further described below in conjunction with the accompanying drawings.
[0027] figure 1It is a plan view of a prefabricated cavity panel forming a two-way force-bearing floor of the present invention. When the present invention is implemented, a prefabricated cavity plate forming a two-way force-bearing floor is determined according to the secondary design decomposition of the architectural design drawings. The production is organized according to the number of decomposed standard parts or special-shaped parts; the prefabricated cavity panel 7 is a prefabricated concrete component, including longitudinal ribs 52 and exposed at both ends of the longitudinal ribs, and two adjacent cavity panels with two-way force are to be formed. The short ribs are connected 51 to form two-way stressed steel bars, and the device 10 is exposed at the ends of the short transverse ribs, and the end positions of the short transverse ribs are temporarily wrapped by frag...
PUM
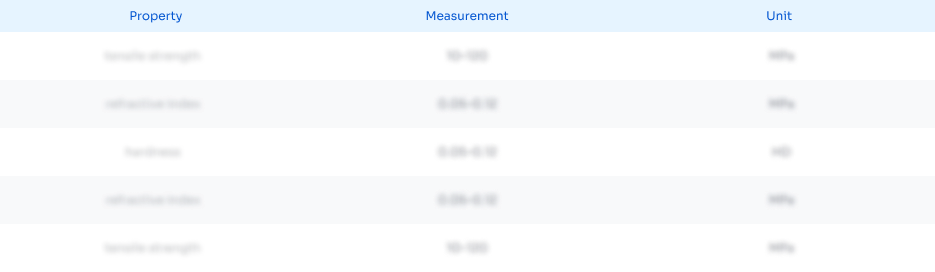
Abstract
Description
Claims
Application Information

- R&D Engineer
- R&D Manager
- IP Professional
- Industry Leading Data Capabilities
- Powerful AI technology
- Patent DNA Extraction
Browse by: Latest US Patents, China's latest patents, Technical Efficacy Thesaurus, Application Domain, Technology Topic, Popular Technical Reports.
© 2024 PatSnap. All rights reserved.Legal|Privacy policy|Modern Slavery Act Transparency Statement|Sitemap|About US| Contact US: help@patsnap.com