Preparation method of weather-resistance tile adhesion agent for exterior wall ceramic tiles
A tile adhesive and weather-resistant technology, which is applied in the field of preparation of weather-resistant tile adhesive for exterior wall tiles, can solve the problems of weak adhesion between tiles and walls, being susceptible to sudden temperature changes, and tile peeling. Achieve the effect of low production cost, simple preparation steps and enhanced adhesion
- Summary
- Abstract
- Description
- Claims
- Application Information
AI Technical Summary
Problems solved by technology
Method used
Examples
example 1
[0018] First, weigh 3kg of bagasse, pour it into a high-pressure reactor, and feed saturated steam into the reactor at a stirring speed of 350r / min and a temperature of 95°C until the pressure in the reactor reaches 3.5MPa. After 10 minutes, open the discharge valve at the bottom of the reaction kettle, so that the materials in the reaction kettle are sprayed into the receiving kettle; after the materials in the receiving kettle are naturally cooled to room temperature, the materials are transferred to a liquid nitrogen freezer, frozen with liquid nitrogen for 2 minutes, and then quickly Pour the frozen material into the ball mill, add zirconia ball milling beads according to the ball-to-material ratio of 30:1, mill for 15 minutes, collect the ball-milled material, transfer it to a vacuum drying oven, and dry it at a temperature of 105°C To constant weight, the bagasse fiber whiskers are obtained; then the bagasse fiber whiskers obtained above are mixed with nano-silicon dioxid...
example 2
[0021]First weigh 4kg of bagasse, pour it into a high-pressure reactor, and at a stirring speed of 375r / min and a temperature of 100°C, feed saturated steam into the reactor until the pressure in the reactor reaches 3.8MPa, and keep the pressure After 13 minutes, open the discharge valve at the bottom of the reaction kettle, so that the materials in the reaction kettle are sprayed into the receiving kettle; after the materials in the receiving kettle are naturally cooled to room temperature, the materials are transferred to a liquid nitrogen freezer and treated with liquid nitrogen for 3 minutes, and then quickly Pour the frozen material into a ball mill, add zirconia ball milling beads according to the ball-to-material ratio of 35:1, and mill for 18 minutes. Collect the ball-milled material, transfer it to a vacuum drying oven, and dry it at a temperature of 108°C. To constant weight, the bagasse fiber whiskers are obtained; then the above-mentioned bagasse fiber whiskers and ...
example 3
[0024] First weigh 5kg of bagasse, pour it into a high-pressure reactor, and feed saturated steam into the reactor at a stirring speed of 400r / min and a temperature of 105°C until the pressure in the reactor reaches 4.0MPa. After 15 minutes, open the discharge valve at the bottom of the reaction kettle, so that the materials in the reaction kettle are sprayed into the receiving kettle; after the materials in the receiving kettle are naturally cooled to room temperature, the materials are transferred to a liquid nitrogen freezer and treated with liquid nitrogen for 4 minutes, and then quickly Pour the frozen material into the ball mill, add zirconia ball milling beads according to the ball-to-material ratio of 40:1, mill for 20 minutes, collect the ball-milled material, transfer it to a vacuum drying oven, and dry it at a temperature of 110°C To constant weight, the bagasse fiber whiskers are obtained; then the bagasse fiber whiskers obtained above are mixed with nano-silicon di...
PUM
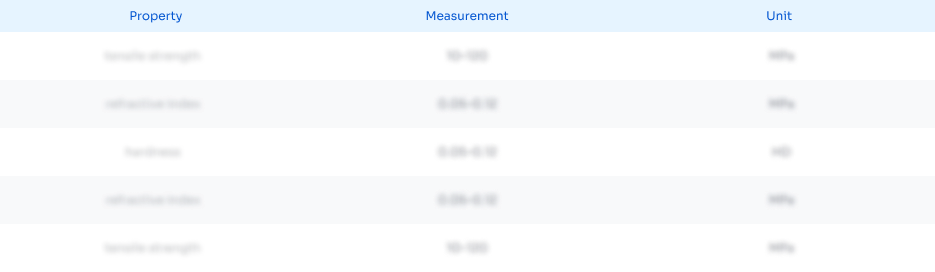
Abstract
Description
Claims
Application Information

- R&D
- Intellectual Property
- Life Sciences
- Materials
- Tech Scout
- Unparalleled Data Quality
- Higher Quality Content
- 60% Fewer Hallucinations
Browse by: Latest US Patents, China's latest patents, Technical Efficacy Thesaurus, Application Domain, Technology Topic, Popular Technical Reports.
© 2025 PatSnap. All rights reserved.Legal|Privacy policy|Modern Slavery Act Transparency Statement|Sitemap|About US| Contact US: help@patsnap.com