A cable type welding wire applied to cmt welding system and cmt welding system
A welding system and cable-type welding wire technology, applied in welding equipment, welding medium, welding equipment, etc., can solve the problems of limited welding wire diameter and low efficiency, achieve good welding effect, reduce costs, and reduce production costs.
- Summary
- Abstract
- Description
- Claims
- Application Information
AI Technical Summary
Problems solved by technology
Method used
Image
Examples
Embodiment 1
[0015] See Figure 1-2 , The present invention provides a technical solution: a cable type welding wire applied to a CMT welding system, comprising a central welding wire 1, a spiral welding wire 2 is arranged on the outer side of the central welding wire 1, and the spiral welding wire 2 is tightly wound around the central welding wire in a spiral manner 1 and the outer side of the spiral welding wire 2 is provided with a protective ring, the spiral welding wire 2 is provided with four sets of sub-welding wire groups 3, and the sub-welding wire groups 3 are arranged tangentially, and the sub-welding wire groups 3 There are first welding wire 4, second welding wire 5, third welding wire 6 and fourth welding wire 7 inside. The diameters of the first welding wire 4 and the second welding wire 5 are D, the third welding wire 6 and the fourth welding wire The diameter of 7 is d, and d is smaller than D. The spiral welding wire 2 is seven strands, and the seven spiral welding wires 2...
Embodiment 2
[0021] See Figure 1-2 , The present invention provides a technical solution: a cable type welding wire applied to a CMT welding system, comprising a central welding wire 1, a spiral welding wire 2 is arranged on the outer side of the central welding wire 1, and the spiral welding wire 2 is tightly wound around the central welding wire in a spiral manner 1 and the outer side of the spiral welding wire 2 is provided with a protective ring, the spiral welding wire 2 is provided with four sets of sub-welding wire groups 3, and the sub-welding wire groups 3 are arranged tangentially, and the sub-welding wire groups 3 There are first welding wire 4, second welding wire 5, third welding wire 6 and fourth welding wire 7 inside. The diameters of the first welding wire 4 and the second welding wire 5 are D, the third welding wire 6 and the fourth welding wire The diameter of 7 is d, and d is smaller than D. The spiral welding wire 2 is seven strands, and the seven spiral welding wires 2...
PUM
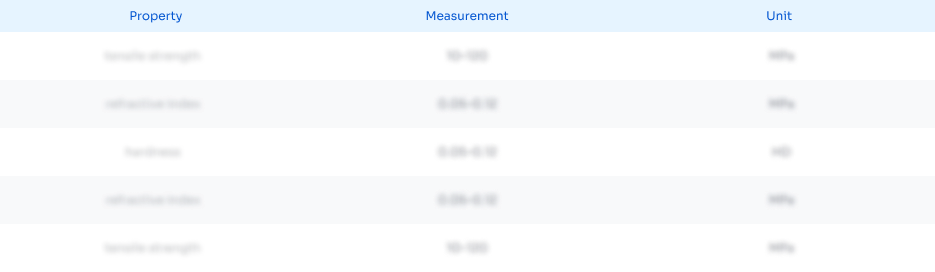
Abstract
Description
Claims
Application Information

- R&D
- Intellectual Property
- Life Sciences
- Materials
- Tech Scout
- Unparalleled Data Quality
- Higher Quality Content
- 60% Fewer Hallucinations
Browse by: Latest US Patents, China's latest patents, Technical Efficacy Thesaurus, Application Domain, Technology Topic, Popular Technical Reports.
© 2025 PatSnap. All rights reserved.Legal|Privacy policy|Modern Slavery Act Transparency Statement|Sitemap|About US| Contact US: help@patsnap.com