Mineral processing technology capable of reducing content of magnesium oxide in flotation concentrates of sulphide copper ores
A technology for flotation of concentrate and copper sulfide, which is applied in flotation, solid separation and other directions, can solve the problems of smelting process, high magnesium oxide content, low copper recovery rate, etc., and achieves good separation effect and less dosage. , improve the effect of selectivity
- Summary
- Abstract
- Description
- Claims
- Application Information
AI Technical Summary
Problems solved by technology
Method used
Image
Examples
Embodiment 1
[0038] like figure 1 Shown, a kind of beneficiation process that reduces magnesium oxide content in copper sulfide ore flotation concentrate comprises the following steps:
[0039] In step (1), the raw copper sulfide ore is ground by a grinding machine. When grinding, lime is added to the grinding machine at the same time. The amount of lime added is 1000 g / t, and the grinding fineness is -74 μm 80%. Obtain raw ore grinding products;
[0040] Step (2), add 60 grams / ton of sodium sulfide, 50 grams / ton of butyl xanthate and 60 grams / ton of 2# oil to the raw ore grinding product obtained in step (1) to carry out roughing of copper sulfide for the first time to obtain copper sulfide Rough concentrate Ⅰ and copper rough tailings Ⅰ;
[0041] Add 30 g / ton of sodium sulfide, 20 g / ton of butyl xanthate and 10 g / ton of 2# oil to copper rough tailings I for the second rough separation of copper sulfide to obtain copper rough concentrate II and copper rough tailings II;
[0042] Add 1...
Embodiment 2
[0046] like figure 1 Shown, a kind of beneficiation process that reduces magnesium oxide content in copper sulfide ore flotation concentrate comprises the following steps:
[0047] In step (1), the raw copper sulfide ore is ground by a grinding machine. When grinding, lime is added to the grinding machine at the same time. The amount of lime added is 1000 g / t, and the grinding fineness is -74 μm 80%. Obtain raw ore grinding products;
[0048] Step (2), add 60 grams / ton of sodium sulfide, 50 grams / ton of butyl xanthate and 60 grams / ton of 2# oil to the raw ore grinding product obtained in step (1) to carry out roughing of copper sulfide for the first time to obtain copper sulfide Rough concentrate Ⅰ and copper rough tailings Ⅰ;
[0049] Add 30 g / ton of sodium sulfide, 20 g / ton of butyl xanthate and 10 g / ton of 2# oil to copper rough tailings I for the second rough separation of copper sulfide to obtain copper rough concentrate II and copper rough tailings II;
[0050] Add 1...
Embodiment 3
[0054] A kind of beneficiation process that reduces magnesium oxide content in copper sulfide ore flotation concentrate, comprises the following steps:
[0055] In step (1), the raw copper sulfide ore is ground by a grinding machine. When grinding, lime is added to the grinding machine at the same time. The amount of lime added is 500 g / ton, and the grinding fineness is -74 μm 75%. Obtain raw ore grinding products;
[0056] In step (2), the raw ore grinding product obtained in step (1) is subjected to copper sulfide flotation, the total amount of sodium sulfide added in the flotation process is 100 grams / ton, the total amount of butyl xanthate is 50 grams / ton and 2 #Oil total amount is 50 grams / ton, obtains copper crude concentrate;
[0057] The flotation includes the second roughing and the first sweeping in sequence, the coarse copper concentrate obtained by the two roughings is merged and then the regrinding process of step (3) is carried out, and the copper sweeping conce...
PUM
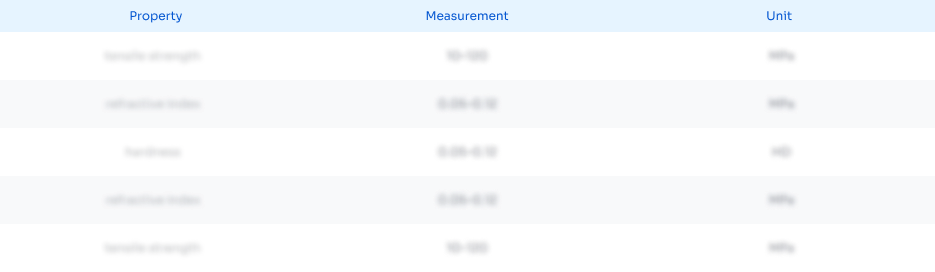
Abstract
Description
Claims
Application Information

- R&D
- Intellectual Property
- Life Sciences
- Materials
- Tech Scout
- Unparalleled Data Quality
- Higher Quality Content
- 60% Fewer Hallucinations
Browse by: Latest US Patents, China's latest patents, Technical Efficacy Thesaurus, Application Domain, Technology Topic, Popular Technical Reports.
© 2025 PatSnap. All rights reserved.Legal|Privacy policy|Modern Slavery Act Transparency Statement|Sitemap|About US| Contact US: help@patsnap.com