Machining method for deep hole of marine engine connecting rod
A marine engine and processing method technology, which is applied to metal processing equipment, metal processing mechanical parts, manufacturing tools, etc., can solve the problems of increasing the production cost of connecting rods, cumbersome clamping operations, low processing efficiency, etc. The effect of easy guarantee of shape and position tolerance and high processing efficiency
- Summary
- Abstract
- Description
- Claims
- Application Information
AI Technical Summary
Problems solved by technology
Method used
Image
Examples
Embodiment Construction
[0021] Below in conjunction with accompanying drawing and embodiment the present invention will be further described:
[0022] Such as image 3 , Figure 4 , Figure 5 As shown, the tooling is composed of a positioning base plate 7, a guide hole positioning plate 8, a first compression module 9, a first compression screw 10, a second compression module 11, a second compression screw 12, and side positioning pins 13. Wherein, positioning base plate 7 is rectangular, guide hole positioning plate 8 is set at the left end of positioning base plate 7, and this guide hole positioning plate 8 is perpendicular to positioning base plate 7, and guiding hole positioning plate 8 is preferably " U " shape, and guiding hole positioning plate 8 The lower end and the left end of the positioning base plate 7 are abutted against and fixed. Two upper and lower guide sleeve holes 8a are respectively opened on the upper parts of the left and right ends of the guide hole positioning plate 8, and...
PUM
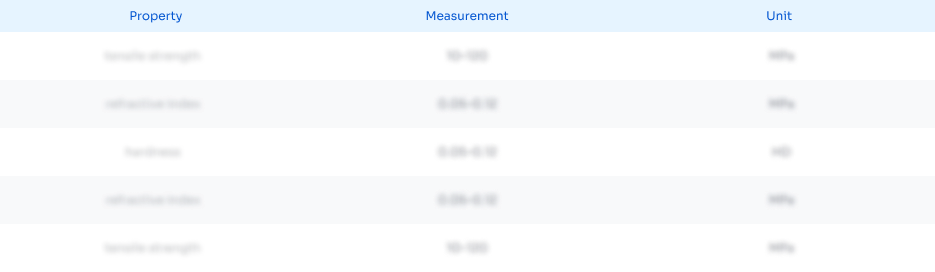
Abstract
Description
Claims
Application Information

- R&D
- Intellectual Property
- Life Sciences
- Materials
- Tech Scout
- Unparalleled Data Quality
- Higher Quality Content
- 60% Fewer Hallucinations
Browse by: Latest US Patents, China's latest patents, Technical Efficacy Thesaurus, Application Domain, Technology Topic, Popular Technical Reports.
© 2025 PatSnap. All rights reserved.Legal|Privacy policy|Modern Slavery Act Transparency Statement|Sitemap|About US| Contact US: help@patsnap.com