Preparation method and application of titanium-silicon composite oxide catalyst
A composite oxide and catalyst technology, which is applied in the direction of catalyst activation/preparation, organic compound/hydride/coordination complex catalyst, physical/chemical process catalyst, etc. It can solve the complicated preparation process, long reaction time, difficult control, etc. problems, to achieve the effect of good catalytic activity, fast decomposition process and easy operation
- Summary
- Abstract
- Description
- Claims
- Application Information
AI Technical Summary
Problems solved by technology
Method used
Image
Examples
Embodiment 1
[0053] Under stirring, 5g TiCl 4 with 3g Mg(NO 3 ) 2 Dissolve in 80 mL of isopropanol. Add 25g of macroporous type C silica gel to the above solution, and soak at 40°C for 12 hours. The above mixture was then passed through an oil bath at 100°C for 3 hours. The obtained catalyst precursor was treated in a flat-plate dielectric barrier discharge plasma discharger for 1 hour using a plasma generator power supply with a power of 50 W and using air as the discharge medium. Then, at 250° C., with high-purity nitrogen as the carrier gas, 3 g of hexamethyldisilazane was passed through for reaction for 1 hour to obtain catalyst B. It was used in reaction kettle and fixed bed propylene epoxidation reaction respectively, and its reaction performance was evaluated. The results are shown in Table 2.
Embodiment 2
[0057] Under stirring, 10g TiCl 4 with 4g Zn(NO 3 ) 2 Dissolve in 100mL ethanol. Add 60g of SBA-15 (Nankai University Catalyst Factory, calculated according to the silicon dioxide content as 100%) to the above solution, and soak at 20°C for 2 hours. The above mixture was then passed through an oil bath at 80 °C for 2 hours. The obtained catalyst precursor was treated in a flat-plate dielectric barrier discharge plasma discharger for 0.5 hours using a plasma generator power supply with a power of 40W and using air as the discharge medium. Afterwards, at 120° C., 1 g of hexamethyldisilazane was passed through with high-purity nitrogen as the carrier gas for 0.5 hour reaction to obtain catalyst C. It was used in reaction kettle and fixed bed propylene epoxidation reaction respectively, and its reaction performance was evaluated. The results are shown in Table 2.
Embodiment 3
[0059] Under stirring, mix 18g tetrabutyl titanate with 3g ZnCl 2 Dissolve in 80mL ethanol. Add 40 g of HMS (Nankai University Catalyst Factory, calculated according to the silicon dioxide content as 100%) to the above solution, and soak at 20° C. for 20 hours. The above mixture was then passed through an oil bath at 80 °C for 1 hour. The obtained catalyst precursor was treated in a flat-plate dielectric barrier discharge plasma discharger for 1.5 hours using a plasma generator power supply with a power of 80W and using air as the discharge medium. Then, at 300° C., with high-purity nitrogen as the carrier gas, 8 g of hexamethyldisilazane was passed through for reaction for 8 hours to obtain catalyst D. It was used in reaction kettle and fixed bed propylene epoxidation reaction respectively, and its reaction performance was evaluated. The results are shown in Table 2.
PUM
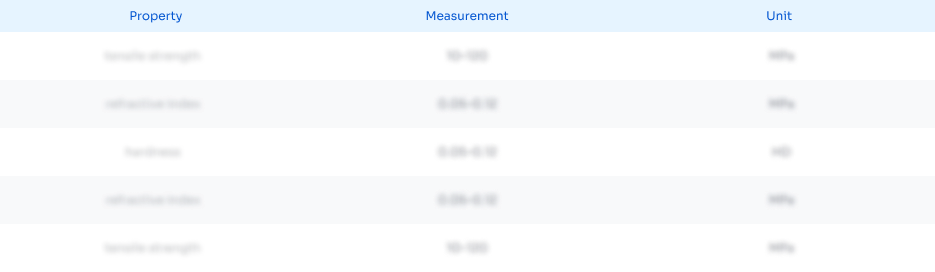
Abstract
Description
Claims
Application Information

- Generate Ideas
- Intellectual Property
- Life Sciences
- Materials
- Tech Scout
- Unparalleled Data Quality
- Higher Quality Content
- 60% Fewer Hallucinations
Browse by: Latest US Patents, China's latest patents, Technical Efficacy Thesaurus, Application Domain, Technology Topic, Popular Technical Reports.
© 2025 PatSnap. All rights reserved.Legal|Privacy policy|Modern Slavery Act Transparency Statement|Sitemap|About US| Contact US: help@patsnap.com