Aluminum alloy bat long in service life
An aluminum alloy, long-life technology, applied in the field of aluminum alloys, can solve the problems of uncoordinated strength, hardness and corrosion resistance, low adhesion between the film layer and aluminum alloy materials, and low corrosion resistance of aluminum alloys, etc., to achieve Increase corrosion resistance and mechanical properties, coordination of corrosion resistance and mechanical properties, mutual effect of corrosion resistance and mechanical properties
- Summary
- Abstract
- Description
- Claims
- Application Information
AI Technical Summary
Problems solved by technology
Method used
Examples
Embodiment 1
[0015] An aluminum alloy ball bat with long service life. The weight percentage of each component is as follows: Si: 0.04%, Fe: 0.04%, Cu: 0.08%, Mn: 0.14%, Mg: 0.8%, Cr: 0.1%, Zn: 0.1%, Ti: 0.04%, Sc: 0.25%, Nd: 0.2%, the balance is Al;
[0016] Among them, Sc*Nd / Mn / Cr=3.57, Sc / Mg+Mg*Zn / Cu=1.3;
[0017] In the process of preparing long-life aluminum alloy ball rods, the aluminum ingot and the remaining raw materials are melted, refined, poured into a solid solution, heated to 440°C, kept for 40 minutes, quenched with water once, cooled to room temperature, and then heated to 440 ℃, keep for 40min, quench twice with water, cool to room temperature, heat up to 150℃, keep for 15h, cool to 120℃, keep for 24h, and cool to room temperature to get long service life aluminum alloy bat.
Embodiment 2
[0019] An aluminum alloy ball bat with long service life, the weight percentage of each component is as follows: Si: 0.05%, Fe: 0.02%, Cu: 0.1%, Mn: 0.1%, Mg: 1%, Cr: 0.08%, Zn: 0.2%, Ti: 0.02%, Sc: 0.3%, Nd: 0.15%, the balance is Al;
[0020] Among them, Sc*Nd / Mn / Cr=5.63, Sc / Mg+Mg*Zn / Cu=2.3;
[0021] In the process of preparing long-life aluminum alloy ball rods, the aluminum ingot and the remaining raw materials are melted, refined, poured into shape, solid solution, heated to 450℃, kept for 30min, quenched with water once, cooled to room temperature, and then heated to 450 ℃, keep for 30min, quench twice with water, cool to room temperature, heat up to 170℃, keep for 10h, cool to 130℃, keep for 20h, and cool to room temperature to get long service life aluminum alloy bat.
Embodiment 3
[0023] An aluminum alloy ball bat with long service life. The weight percentage of each component is as follows: Si: 0.042%, Fe: 0.035%, Cu: 0.085%, Mn: 0.13%, Mg: 0.85%, Cr: 0.095%, Zn: 0.13%, Ti: 0.035%, Sc: 0.26%, Nd: 0.19%, the balance is Al;
[0024] Among them, Sc*Nd / Mn / Cr=4, Sc / Mg+Mg*Zn / Cu=1.61;
[0025] In the process of preparing long-life aluminum alloy ball bars, the aluminum ingot and the remaining raw materials are melted, refined, poured into shape, and dissolved, heated to 442°C, held for 38 minutes, quenched with water once, cooled to room temperature, and then heated to 442 ℃, keep for 38min, quench twice with water, cool to room temperature, warm up to 155℃, keep for 14h, cool to 123℃, keep for 23h, air-cool to room temperature to obtain aluminum alloy bat with long service life.
PUM
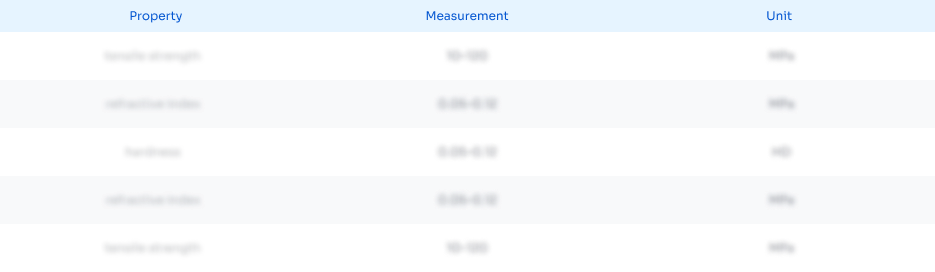
Abstract
Description
Claims
Application Information

- R&D Engineer
- R&D Manager
- IP Professional
- Industry Leading Data Capabilities
- Powerful AI technology
- Patent DNA Extraction
Browse by: Latest US Patents, China's latest patents, Technical Efficacy Thesaurus, Application Domain, Technology Topic, Popular Technical Reports.
© 2024 PatSnap. All rights reserved.Legal|Privacy policy|Modern Slavery Act Transparency Statement|Sitemap|About US| Contact US: help@patsnap.com