Hydrolysis technology and device for concentrated hydrochloric acid
A concentrated acid hydrolysis and hydrolysis device technology, applied in organic chemistry, silicon organic compounds, chemical instruments and methods, etc., can solve problems affecting the normal operation of equipment, unfavorable oil-water separation, and decrease in ring yield, so as to improve reaction efficiency and product quality, improved separation, and reduced coagulation
- Summary
- Abstract
- Description
- Claims
- Application Information
AI Technical Summary
Problems solved by technology
Method used
Image
Examples
Embodiment 1
[0018] Control the hydrolysis reaction between dimethyldichlorosilane and concentrated hydrochloric acid in a static mixer at 35°C and 0.2MPa, and the resulting gas-liquid mixture enters the gas-liquid separation tank A (1) for separation, and the gas-liquid separation tank A (1 ) The gas produced at the top enters the Venturi mixer (2) and is fully mixed with the concentrated hydrochloric acid main fluid. The mass concentration of the concentrated hydrochloric acid is 38%, and the mass ratio of the concentrated acid to the gas mixture is 1:3. The gas-liquid separation tank B (3) is separated, the liquid extracted from the bottom of the gas-liquid separation tank B (3) is returned to the Venturi mixer through the material pump, and the gas extracted from the top is passed through the primary condenser (4) and the secondary condenser (5) The final temperature is -10°C and the pressure is 0.15MPa. The liquid extracted from the bottom of the gas-liquid separation tank (1) and the...
Embodiment 2
[0020] Control the hydrolysis reaction between dimethyldichlorosilane and concentrated hydrochloric acid in a static mixer at 35°C and 0.2MPa, and the resulting gas-liquid mixture enters the gas-liquid separation tank A (1) for separation, and the gas-liquid separation tank A (1 ) The gas produced at the top enters the Venturi mixer (2) and is fully mixed with the concentrated hydrochloric acid main fluid. The mass concentration of the concentrated hydrochloric acid is 38%, and the mass ratio of the concentrated acid to the gas mixture is 1:4. The gas-liquid separation tank B (3) is separated, the liquid extracted from the bottom of the gas-liquid separation tank B (3) is returned to the Venturi mixer through the material pump, and the gas extracted from the top is passed through the primary condenser (4) and the secondary condenser (5) The final temperature is 0°C and the pressure is 0.20MPa. The liquid extracted from the bottom of the gas-liquid separation tank (1) and the c...
Embodiment 3
[0022] Control the hydrolysis reaction between dimethyldichlorosilane and concentrated hydrochloric acid in a static mixer at 35°C and 0.2MPa, and the resulting gas-liquid mixture enters the gas-liquid separation tank A (1) for separation, and the gas-liquid separation tank A (1 ) The gas produced at the top enters the Venturi mixer (2) and is fully mixed with the concentrated hydrochloric acid main fluid. The mass concentration of the concentrated hydrochloric acid is 38%, and the mass ratio of the concentrated acid to the gas mixture is 1:5. The gas-liquid separation tank B (3) is separated, the liquid extracted from the bottom of the gas-liquid separation tank B (3) is returned to the Venturi mixer through the material pump, and the gas extracted from the top is passed through the primary condenser (4) and the secondary condenser (5) The final temperature is 10°C and the pressure is 0.25MPa. The liquid extracted from the bottom of the gas-liquid separation tank (1) and the ...
PUM
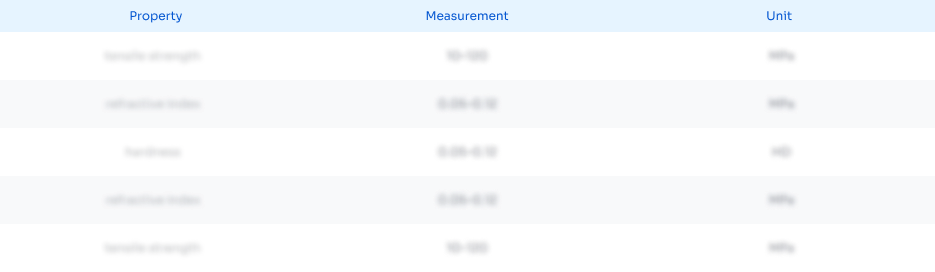
Abstract
Description
Claims
Application Information

- Generate Ideas
- Intellectual Property
- Life Sciences
- Materials
- Tech Scout
- Unparalleled Data Quality
- Higher Quality Content
- 60% Fewer Hallucinations
Browse by: Latest US Patents, China's latest patents, Technical Efficacy Thesaurus, Application Domain, Technology Topic, Popular Technical Reports.
© 2025 PatSnap. All rights reserved.Legal|Privacy policy|Modern Slavery Act Transparency Statement|Sitemap|About US| Contact US: help@patsnap.com