Lightweight carbon fiber cable climbing robot with detection system and its method for cable detection
A detection system, carbon fiber technology, applied in bridge maintenance, bridge parts, erection/assembly of bridges, etc., can solve problems such as unfavorable low-order frequency identification, poor accuracy, wire bundle or steel strand corrosion, etc., to increase cable force detection. function, improve accuracy, increase the effect of the contact surface
- Summary
- Abstract
- Description
- Claims
- Application Information
AI Technical Summary
Problems solved by technology
Method used
Image
Examples
Embodiment 1
[0039] A light carbon fiber climbing rope robot with detection system
[0040] like Figure 1-1~Figure 1-2 As shown, the light carbon fiber climbing rope robot with a detection system includes a crawling mechanism, a control unit 2, a power system, a video acquisition unit 6, a wireless data transmission unit 9 and a detection mechanism;
[0041] like Figure 2-1~Figure 2-2 As shown, the crawling mechanism includes two halves of light carbon fiber frames 11, a pair of driving wheels 12 and a pair of driven wheels 13, and the two halves of light carbon fiber frames 11 are composed of four pairs of connecting arms 111 and two carbon fiber mounting plates 112 There is an installation window on the carbon fiber mounting plate; a pair of driving wheels and a pair of driven wheels are driven by two-sided clamping 4-wheel dual motors, and are connected by four pairs of connecting arms 111 by using a two-half light carbon fiber frame 11 structure; It is not only convenient to load a...
Embodiment 2
[0048] A method for cable detection, which uses the light carbon fiber cable-climbing robot with a detection system described in Embodiment 1 to be used for cable detection, and its steps include:
[0049] A. Install the cable-climbing robot: install the light-duty carbon fiber cable-climbing robot with detection system of the present invention on the bottom of the boom or stay cable, open the detection software system on the host computer, identify and set the wireless network; test the initial value on the software And store, set the crawling speed;
[0050] B. Turn on the measurement, and the cable-climbing robot crawls along the cable:
[0051] B1: Detect the PE appearance of the cable and the corrosion of broken wires: the cable climbing robot automatically starts to crawl along the cable, and detects the PE appearance of the cable and the rust of broken wires in real time;
[0052] B2: Measuring the cable force value: When the cable climbing robot travels to 1 / 4 of the ...
PUM
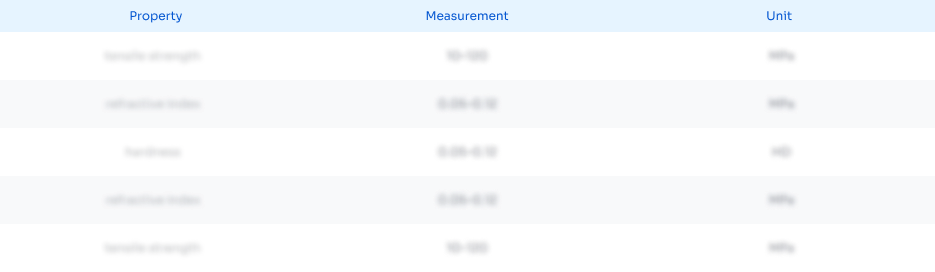
Abstract
Description
Claims
Application Information

- R&D Engineer
- R&D Manager
- IP Professional
- Industry Leading Data Capabilities
- Powerful AI technology
- Patent DNA Extraction
Browse by: Latest US Patents, China's latest patents, Technical Efficacy Thesaurus, Application Domain, Technology Topic, Popular Technical Reports.
© 2024 PatSnap. All rights reserved.Legal|Privacy policy|Modern Slavery Act Transparency Statement|Sitemap|About US| Contact US: help@patsnap.com