A method for improving the pulverization rate of low-temperature reduction of sintered ore
A technology of pulverization rate and sintering ore, which is applied in the field of improving the reduction pulverization rate of sintering ore, can solve problems such as reducing production costs, and achieve the effects of reducing production costs, prolonging sintering time, and improving metallurgical performance indicators
- Summary
- Abstract
- Description
- Claims
- Application Information
AI Technical Summary
Problems solved by technology
Method used
Image
Examples
Embodiment 1
[0017] The mass percentage is 78% of magnetite and 19% of flux (8% of quicklime, 1.9% of limestone, 2% of magnesium stone) and 1.86% of coke powder (solid fuel is 3%, of which coking and dust removal 38% of the solid fuel, and coke powder accounts for 62% of the solid fuel) are mixed, and then the mixed material is sieved according to three particle size levels of 5mm. Mix the sieved mixture 3 / h; after the mixture is sprayed with coking dust and atomized water, the mass percentage of water is controlled at 7.2%. When distributing materials, arrange the sintered mixture with a particle size of >5mm at the bottom of the material layer, arrange the mixture with an original particle size of 3mm-5mm and added coking dust in the middle of the material layer, and place the original particle size at the middle of the material layer. The mixed material with a diameter of <3 mm and added with coking and dedusting ash is arranged on the uppermost part of the material layer, and finally ...
Embodiment 2
[0022] The mass percentage is 80% hematite and 15.5% flux (6% quicklime, 8% limestone, 1.5% magnesite) and 3.285% coke powder (solid fuel is 4.5%, wherein coking dedusting ash accounts for 27% of the solid fuel, coke powder accounts for 73% of the solid fuel) are mixed, and then the mixed material is sieved according to three particle size levels of 5mm. Mix the sieved mixture 3 / h; after the mixture is sprayed with coking dust and atomized water, the mass percentage of water is controlled at 7.7%. When distributing materials, arrange the sintered mixture with a particle size of >5mm at the bottom of the material layer, arrange the mixture with an original particle size of 3mm-5mm and added coking dust in the middle of the material layer, and place the original particle size at the middle of the material layer. The mixed material with a diameter of <3 mm and added with coking and dedusting ash is arranged on the uppermost part of the material layer, and finally sintered to obt...
Embodiment 3
[0027]The mass percentage is 84% limonite and 10.6% flux (3% quicklime, 5.5% limestone, 1.0% magnesite) and 5.2% coke powder (solid fuel is 6.5%, wherein coking dedusting ash accounts for 20% of the solid fuel, and coke powder accounts for 80% of the solid fuel) are mixed, and then the mixed material is sieved according to three particle size levels of 5mm. Mix the sieved mixture 3 / h; after the mixture is sprayed with coking dust and atomized water, the mass percentage of water is controlled at 7.5%. When distributing materials, arrange the sintered mixture with a particle size of >5mm at the bottom of the material layer, arrange the mixture with an original particle size of 3mm-5mm and added coking dust in the middle of the material layer, and place the original particle size at the middle of the material layer. The mixed material with a diameter of <3 mm and added with coking and dedusting ash is arranged on the uppermost part of the material layer, and finally sintered t...
PUM
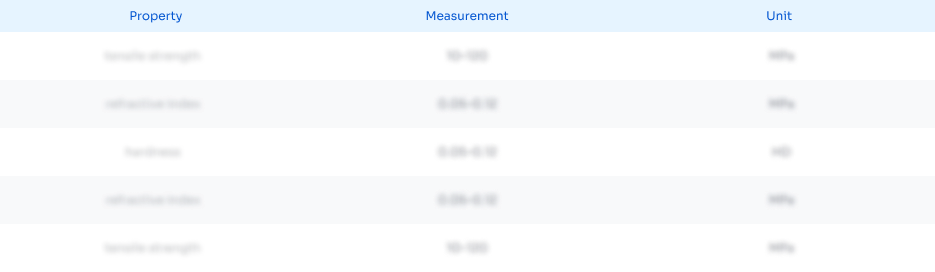
Abstract
Description
Claims
Application Information

- R&D
- Intellectual Property
- Life Sciences
- Materials
- Tech Scout
- Unparalleled Data Quality
- Higher Quality Content
- 60% Fewer Hallucinations
Browse by: Latest US Patents, China's latest patents, Technical Efficacy Thesaurus, Application Domain, Technology Topic, Popular Technical Reports.
© 2025 PatSnap. All rights reserved.Legal|Privacy policy|Modern Slavery Act Transparency Statement|Sitemap|About US| Contact US: help@patsnap.com