Method for welding outgoing line terminal of nuclear power half-speed turbine generator
A technology for turbogenerators and outgoing terminals, applied in welding equipment, arc welding equipment, manufacturing tools, etc., can solve the problem of affecting welding quality, affecting the manufacturing level of nuclear half-speed turbogenerators, and affecting the product quality and production of outgoing terminals Efficiency and other issues to achieve the effect of improving welding quality, reducing the chance of repair, and concentrating energy
- Summary
- Abstract
- Description
- Claims
- Application Information
AI Technical Summary
Problems solved by technology
Method used
Image
Examples
Embodiment 1
[0018] Embodiment 1: as figure 1 , figure 2 As shown, the welding method for the outlet terminals of nuclear power half-speed turbogenerators in this embodiment, the method is completed according to the following steps:
[0019] Step 1. Material preparation: the seat board 1 and the terminal board 2 are cut by plasma cutting, and the cutting is flattened by a hydraulic machine. The flattening process is protected by gaskets of the same material, and each single piece is processed to a qualified size;
[0020] Step 2, scribing: taking the center line of the seat plate 1 determined during the processing of step 1 as the reference, draw the assembly position line of the terminal plate 2 on the seat plate 1;
[0021] Step 3. Assembly: Assemble the terminal board (2) on the seat board 1 according to the assembly position line drawn in step 2. The distance from the terminal board 2 to the center of the seat board 1 is enlarged by 2~3mm according to the nominal size for assembly, a...
Embodiment 2
[0028] Embodiment 2: as figure 1 , figure 2 As shown, in step 7 of this embodiment, when welding the head weld 5, the local weld requires tungsten inert gas shielded welding TIG welding for end head welding, and the welding material is Φ2.5mm and the model is ERCuNi-7 Welding wire, welding current is 230A, welding voltage is 24V, shielding gas is more than 99.997% high-purity helium, gas flow rate is 14L / min. Other steps are the same as in Example 1.
Embodiment 3
[0029] Embodiment 3: The base plate 1 and the terminal plate 2 of this embodiment are copper plates whose material type is T2Y1. Other steps are identical with embodiment 1,2.
PUM
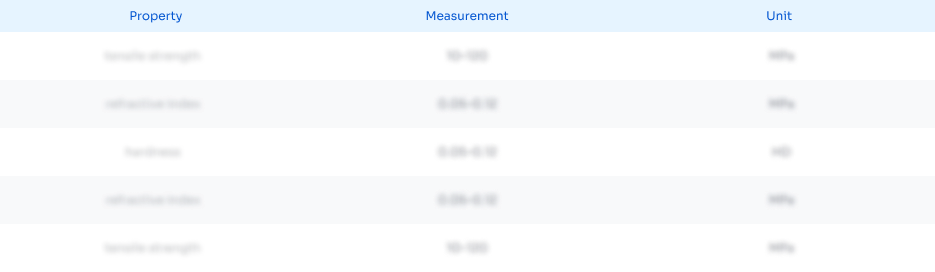
Abstract
Description
Claims
Application Information

- R&D Engineer
- R&D Manager
- IP Professional
- Industry Leading Data Capabilities
- Powerful AI technology
- Patent DNA Extraction
Browse by: Latest US Patents, China's latest patents, Technical Efficacy Thesaurus, Application Domain, Technology Topic, Popular Technical Reports.
© 2024 PatSnap. All rights reserved.Legal|Privacy policy|Modern Slavery Act Transparency Statement|Sitemap|About US| Contact US: help@patsnap.com