Forming technological method for high-ferrum bearing ring with metal flow lines distributed along roller path
A metal streamline and forming process technology, applied to bearing components, shafts and bearings, mechanical equipment, etc., can solve the problems of low material utilization rate and metal streamline cannot be distributed, and achieve the effect of improving utilization rate
- Summary
- Abstract
- Description
- Claims
- Application Information
AI Technical Summary
Problems solved by technology
Method used
Image
Examples
Embodiment Construction
[0024] In order to have a clearer understanding of the technical features, purposes and effects of the present invention, the specific implementation manners of the present invention will now be described in detail with reference to the accompanying drawings.
[0025] Such as Figure 7 As shown, the process flow of the high-speed rail bearing ring forming process in which the metal flow lines are distributed along the raceway of the present invention is: pier thickening, blind hole punching, hot forging billet → ordinary hot-rolled near-conical outer ring and inner ring → precision close-shaped The hot-rolled high-speed rail bearing ring raceway profile forms metal streamlines distributed along the raceway (such as Figure 6a , Figure 6b shown) → deformation heat treatment → grinding → superfinishing. Specifically include the following steps:
[0026] S1. After the ordinary hot-rolled near-conical outer ring and inner ring process, add a process of precision close-shaped h...
PUM
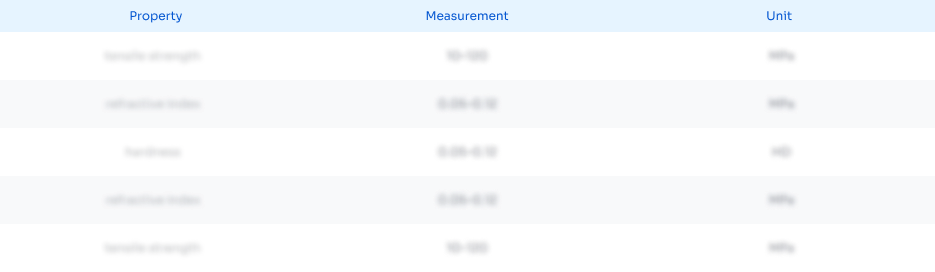
Abstract
Description
Claims
Application Information

- Generate Ideas
- Intellectual Property
- Life Sciences
- Materials
- Tech Scout
- Unparalleled Data Quality
- Higher Quality Content
- 60% Fewer Hallucinations
Browse by: Latest US Patents, China's latest patents, Technical Efficacy Thesaurus, Application Domain, Technology Topic, Popular Technical Reports.
© 2025 PatSnap. All rights reserved.Legal|Privacy policy|Modern Slavery Act Transparency Statement|Sitemap|About US| Contact US: help@patsnap.com