Charing and gasification composite furnace
A technology of carbonization and gas, which is applied in the direction of gasification process, gasification catalyst, gasification device feeding tool, etc., can solve the problems of difficulty, high efficiency and reasonable utilization, and achieve the goal of avoiding the leaching of heavy metals, increasing the moisture content, and avoiding dust. Effect
- Summary
- Abstract
- Description
- Claims
- Application Information
AI Technical Summary
Problems solved by technology
Method used
Image
Examples
Embodiment 1
[0033] Such as figure 1 As shown, the carbonization and gasification compound furnace includes three stages of pyrolysis channels 3 , flue gas channels 4 , oil and gas separators 5 and gas combustion furnaces 6 . The first pyrolysis channel 3 is provided with a feed port 2 and an exhaust port 18, the second pyrolysis channel 3 is provided with an oil return port 21, and the third pyrolysis channel 3 is provided with a volatile matter guide. Outlet 19 and carbon discharge port 20, each pyrolysis channel 3 forms a multi-section sleeve with the corresponding flue gas channel 4. The steam exhaust port 18 is located on the first pyrolysis channel 3 with the feed port 2, and the oil return port 21 is located in the middle and rear section of the second pyrolysis channel; the volatile matter outlet 19 It is located in front of the carbon discharge port 20 and is connected to the inlet of the oil-gas separator 5 through a pipeline; the oil cavity at the lower part of the oil-gas sep...
Embodiment 2
[0037] Such as figure 2 As shown, the carbonization and gasification composite furnace includes four stages of pyrolysis channels 3 , flue gas channels 4 , oil and gas separators 5 and gas combustion furnaces 6 . The pyrolysis channel 3 in the first section is provided with a feed port 2 and an exhaust port 18, the pyrolysis channel 3 in the third section is provided with an oil return port 21, and the pyrolysis channel 3 in the fourth section is provided with a volatile matter guide. Outlet 19 and carbon discharge port 20, each pyrolysis channel 3 forms a multi-section sleeve with the corresponding flue gas channel 4. The steam exhaust port 18 is located on the first-stage pyrolysis channel 3 with the feed port 2, the oil return port 21 is located on the third-stage pyrolysis channel; the volatile matter export port 19 is located on the carbon discharge channel The front of the port 20 is connected with the inlet of the oil-gas separator 5 through a pipeline; the oil cavity...
Embodiment 3
[0041] Such as figure 2 As shown, the carbonization and gasification composite furnace includes four stages of pyrolysis channels 3 , flue gas channels 4 , oil and gas separators 5 , and gas combustion furnaces 6 . The multi-stage pyrolysis channel 3 is provided with a feed port 2, a steam exhaust port 18, an oil return port 21, a volatile matter export port 19, and a carbon discharge port 20, and forms a multi-section sleeve with the flue gas channel 4. The steam exhaust port 18 is located on the pyrolysis channel 3 with the feed port 2, the oil return port 21 is located in the front section of the third stage pyrolysis channel; the volatile matter outlet 19 is located at the carbon discharge port 20 The front of the oil-gas separator 5 is connected with the inlet of the oil-gas separator 5 through a pipeline; the oil cavity at the bottom of the oil-gas separator 5 is connected to the oil return port 21 on the pyrolysis passage 3 through an oil pump 9 and a pipeline; The ai...
PUM
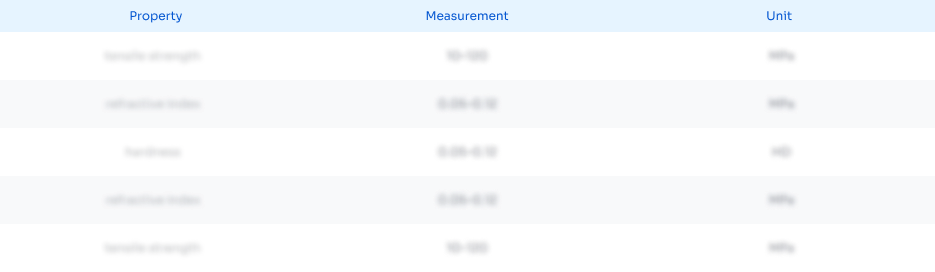
Abstract
Description
Claims
Application Information

- R&D
- Intellectual Property
- Life Sciences
- Materials
- Tech Scout
- Unparalleled Data Quality
- Higher Quality Content
- 60% Fewer Hallucinations
Browse by: Latest US Patents, China's latest patents, Technical Efficacy Thesaurus, Application Domain, Technology Topic, Popular Technical Reports.
© 2025 PatSnap. All rights reserved.Legal|Privacy policy|Modern Slavery Act Transparency Statement|Sitemap|About US| Contact US: help@patsnap.com