A method for synchronous oxidation and separation of phosphorus and vanadium in vanadium-containing molten iron in a converter
A technology for separating phosphorus, vanadium, and converters, which is applied in the manufacture of converters, etc., can solve the problems of affecting the life of converters, the dephosphorization effect is not obvious, and the lining is eroded, so as to reduce the dephosphorization task and facilitate dephosphorization and vanadium extraction. Effect of reducing TFe content
- Summary
- Abstract
- Description
- Claims
- Application Information
AI Technical Summary
Problems solved by technology
Method used
Examples
Embodiment 1
[0020] After the 200t vanadium extracting converter has mixed iron, the temperature of the molten iron is measured at 1310°C. After the temperature measurement is completed, the oxygen-reducing lance is used for blowing, and the oxygen flow rate is controlled at 1.5Nm throughout the process. 3 / t.min, the intensity of bottom blowing nitrogen is 0.3Nm 3 / t.min control; add lime at the beginning of blowing to control the binary alkalinity of the slag at about 1.4; 2 minutes before blowing, the gun position should be 10mm above the reference gun position; 25kg / tFe is controlled, and the oxygen lance is lowered to the reference lance position at the same time; the oxygen lance position is controlled to 30mm above the reference lance position 2 minutes before the end of blowing; semi-steel and vanadium slag are discharged after blowing.
[0021] The vanadium content in molten iron is 0.330%, and the phosphorus content is 0.070%. After blowing, the semi-steel has a vanadium content ...
Embodiment 2
[0023] After the 120t vanadium extracting converter has mixed iron, the temperature of the molten iron is measured at 1280°C. After the temperature measurement is completed, the oxygen-reducing lance is used for blowing, and the oxygen flow rate is controlled at 3.0Nm throughout the process. 3 / t.min, the intensity of bottom blowing nitrogen is 0.2Nm 3 / t.min control; add lime at the beginning of blowing to control the binary alkalinity of the slag at about 1.7; 2 minutes before blowing, the gun position should be 20mm above the reference gun position; 20kg / tFe is controlled, and the oxygen lance is lowered to the reference lance position at the same time; the oxygen lance position is controlled to 40mm above the reference lance position 2 minutes before the end of blowing; semi-steel and vanadium slag are discharged after blowing.
[0024] The vanadium content in molten iron is 0.302%, and the phosphorus content is 0.081%. After blowing, the semi-steel has a vanadium content ...
Embodiment 3
[0026] After the 200t vanadium extracting converter has mixed iron, the temperature of the molten iron is measured at 1250°C. After the temperature measurement is completed, the oxygen-reducing lance is used for blowing, and the oxygen flow rate is controlled at 2Nm throughout the process. 3 / t.min, the intensity of bottom blowing nitrogen is 0.4Nm 3 / t.min control; add lime to control the binary alkalinity of the slag at about 1.7 at the same time of blowing; 2 minutes before blowing, the gun position should be 30mm above the reference gun position; 15kg / tFe is controlled, and the oxygen lance is lowered to the reference lance position at the same time; the oxygen lance position is controlled to 50mm above the reference lance position 2 minutes before the end of blowing; semi-steel and vanadium slag are discharged after blowing.
[0027] The vanadium content in molten iron is 0.386%, and the phosphorus content is 0.061%. After blowing, the semi-steel has a vanadium content of...
PUM
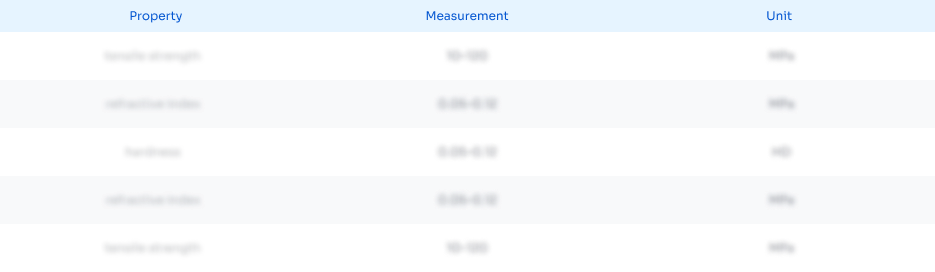
Abstract
Description
Claims
Application Information

- R&D Engineer
- R&D Manager
- IP Professional
- Industry Leading Data Capabilities
- Powerful AI technology
- Patent DNA Extraction
Browse by: Latest US Patents, China's latest patents, Technical Efficacy Thesaurus, Application Domain, Technology Topic, Popular Technical Reports.
© 2024 PatSnap. All rights reserved.Legal|Privacy policy|Modern Slavery Act Transparency Statement|Sitemap|About US| Contact US: help@patsnap.com