High-performance foamed-concrete cement material and preparing method thereof
A technology of foamed concrete and cement materials, applied in the field of chemical materials, can solve the problems of large variation coefficient of fly ash quality, poor concrete effect, poor concrete workability, etc., achieve excellent fire performance, meet clean production and environmental protection requirements, The effect of reducing the amount of cement
- Summary
- Abstract
- Description
- Claims
- Application Information
AI Technical Summary
Problems solved by technology
Method used
Examples
Embodiment 1
[0025] A high-performance foamed concrete cement material, which contains the following components in parts by weight: 30 parts of mineral admixture, 50 parts of cement, 3 parts of retarder, 9 parts of foaming agent, 2 parts of cell wall Strengthening agent, 2 parts of foaming speed regulator, 7.5 parts of magnesium hydroxide, 7.5 parts of aluminum hydroxide and 10 parts of construction mortar admixture;
[0026] Wherein, the mineral admixture is fly ash, tailings powder, mineral powder, stone powder, sludge powder, silica fume, phosphogypsum and calcium carbonate according to 2:1:1:2:2:1:1:1 The mixed powder obtained by uniformly mixing the weight ratio, the cement is Portland cement, and the retarder is boric acid, lithium carbonate, nitrite, chromate, urea according to 2:1:1:1: The mixed powder obtained by uniformly mixing the weight ratio of 2, the foaming agent is the mixed powder obtained by uniformly mixing magnesium powder, aluminum powder and sodium bicarbonate accord...
Embodiment 2
[0029] A high-performance foamed concrete cement material, which contains the following components in parts by weight: 20 parts of mineral admixture, 35 parts of cement, 2 parts of retarder, 6 parts of foaming agent, 1 part of cell wall Strengthening agent, 1 part of foaming speed regulator, 5 parts of magnesium hydroxide, 5 parts of aluminum hydroxide and 5 parts of construction mortar admixture;
[0030] Wherein, the mineral admixture is fly ash, tailings powder, mineral powder, stone powder, sludge powder, silica fume, phosphogypsum, calcium carbonate according to 3:1:2:1:2:1:1:2 The mixed powder obtained by uniformly mixing the weight ratio, the cement is obtained by uniformly mixing Portland cement and slag cement according to the weight ratio of 3:1, and the retarder is boric acid, lithium carbonate, nitrite, The mixed powder obtained by uniformly mixing chromate and urea according to the weight ratio of 3:1:1:1:2, and the foaming agent is magnesium powder, aluminum powd...
Embodiment 3
[0033] A high-performance foamed concrete cement material, which contains the following components in parts by weight: 40 parts of mineral admixtures, 65 parts of cement, 4 parts of retarders, 12 parts of foaming agents, and 3 parts of cell walls Strengthening agent, 3 parts of foaming speed regulator, 10 parts of magnesium hydroxide, 10 parts of aluminum hydroxide and 15 parts of construction mortar admixture;
[0034] Wherein, the mineral admixture is fly ash, tailings powder, mineral powder, stone powder, sludge powder, silica fume, phosphogypsum, calcium carbonate according to 1:1:1:1:1:1:1:1 The mixed powder obtained by uniformly mixing the weight ratio, the cement is obtained by uniformly mixing Portland cement and slag cement according to the weight ratio of 2:1, and the retarder is boric acid, lithium carbonate, nitrite, The mixed powder obtained by uniformly mixing chromate and urea according to the weight ratio of 1:1:1:1:1, and the foaming agent is magnesium powder,...
PUM
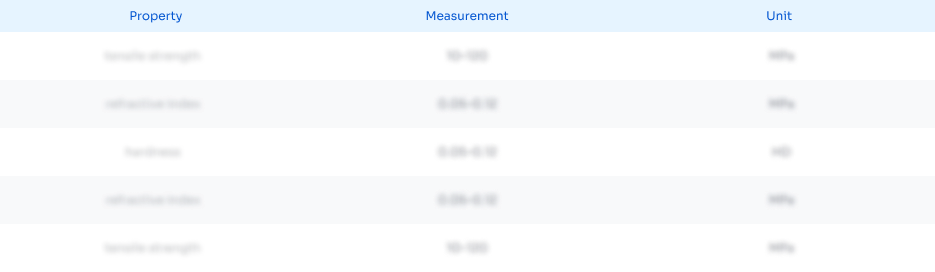
Abstract
Description
Claims
Application Information

- R&D
- Intellectual Property
- Life Sciences
- Materials
- Tech Scout
- Unparalleled Data Quality
- Higher Quality Content
- 60% Fewer Hallucinations
Browse by: Latest US Patents, China's latest patents, Technical Efficacy Thesaurus, Application Domain, Technology Topic, Popular Technical Reports.
© 2025 PatSnap. All rights reserved.Legal|Privacy policy|Modern Slavery Act Transparency Statement|Sitemap|About US| Contact US: help@patsnap.com