PU matte white finish stable in gloss and permanently smooth and preparation method thereof
A white topcoat, permanent technology, applied in coatings, polyester coatings, etc., can solve the problems of uneven gloss of the paint film, blooming, ordinary PU matte clear can not meet the needs of high-end coating, etc., to achieve stable gloss, Good instant leveling effect
- Summary
- Abstract
- Description
- Claims
- Application Information
AI Technical Summary
Problems solved by technology
Method used
Image
Examples
Embodiment 1
[0036] Prepare 60% solid content white paste: first take 34.6% of short oil alkyd resin, 0.2% of fumed silica, 4% of xylene and 1.2% of dispersant (copolymer solution containing acidic groups) and mix by weight percentage. Disperse at 800 rpm for 7 minutes, then add 60% rutile titanium dioxide at 600 rpm, stir and disperse at 1200 rpm for 18 minutes, and finally grind to fineness ≤ 20um.
[0037] Preparation of component A: add 60% solid content white pulp 45%, short oil alkyd resin 13%, 6900-20X anti-settling wax 5%, anti-settling mud 2%, and modified polyurethane in the dispersion tank according to the weight percentage. Polymer dispersant 1.7%, silicone leveling agent 0.2%, defoamer (a solution of foam-breaking polymer and polysiloxane) 0.3% and MIBK 1.5%, stir at 600r / min until uniform, then add poly Tetrafluoroethylene wax powder 0.3% and ED-30 matte powder 1%, stir and disperse at 1200r / min for 15min until the fineness is ≤25um, and then add 20% solid content chlorinated vi...
Embodiment 2
[0042] Prepare 60% solid content white paste: first take 34.6% of short oil alkyd resin, 0.2% of fumed silica, 4% of xylene and 1.2% of dispersant (copolymer solution containing acidic groups) and mix by weight percentage. Disperse for 3 minutes at 1000 rpm, then add 60% rutile titanium dioxide at 800 rpm, stir and disperse at 1500 rpm for 12 minutes, and finally grind to fineness ≤ 20um.
[0043] Preparation of component A: Add 60% solid content of white pulp 52.6%, short oil alkyd resin 12%, 6900-20X anti-wax 4%, anti-settling 1.8%, and modified polyurethane in the dispersion tank according to weight percentage. Polymer dispersant 1.5%, silicone leveling agent 0.3%, defoamer (a solution of foam-breaking polymer and polysiloxane) 0.4% and MIBK 1.2%, stir at 700r / min until uniform, then add polytetrafluoroethylene Vinyl fluoride wax powder 0.4% and ED-30 matte powder 0.8%, stir and disperse at 1300r / min for 13 minutes to a fineness of ≤25um, and then add 20% solid content 12% vin...
Embodiment 3
[0048] Prepare 60% solid content white paste: first take 34.6% of short oil alkyd resin, 0.2% of fumed silica, 4% of xylene and 1.2% of dispersant (copolymer solution containing acidic groups) and mix by weight percentage. Disperse for 5 minutes at 900 rpm, then add 60% rutile titanium dioxide at 700 rpm, stir and disperse at 1300 rpm for 15 minutes, and finally grind to fineness ≤ 20um.
[0049] Preparation of component A: add 60% solid content white pulp 60%, short oil alkyd resin 10%, 6900-20X anti-wax 3.5%, anti-settling 1.5%, and modified polyurethane in the dispersion tank according to weight percentage. Polymer dispersant 1%, silicone leveling agent 0.5%, defoamer (a solution of foam-breaking polymer and polysiloxane) 0.5% and MIBK 1.0%, stir at 800r / min until uniform, then add polytetrafluoroethylene Vinyl fluoride wax powder 0.5% and ED-30 matte powder 0.5%, stir and disperse at 1500r / min for 10min until the fineness is ≤25um, and then add 20% solid content chlorovinegar...
PUM
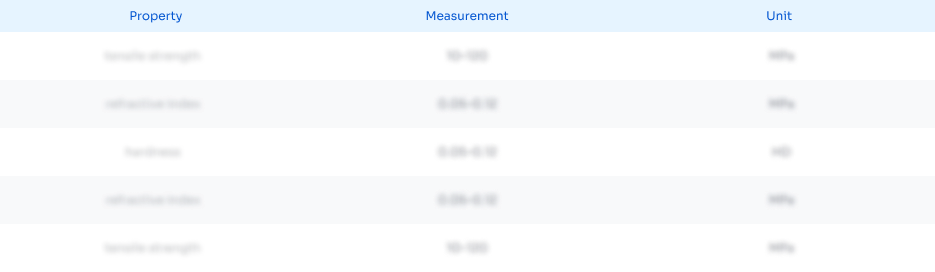
Abstract
Description
Claims
Application Information

- R&D
- Intellectual Property
- Life Sciences
- Materials
- Tech Scout
- Unparalleled Data Quality
- Higher Quality Content
- 60% Fewer Hallucinations
Browse by: Latest US Patents, China's latest patents, Technical Efficacy Thesaurus, Application Domain, Technology Topic, Popular Technical Reports.
© 2025 PatSnap. All rights reserved.Legal|Privacy policy|Modern Slavery Act Transparency Statement|Sitemap|About US| Contact US: help@patsnap.com