Processing device for air inlet cylinder cover
A technology for air intake cylinder heads and processing devices, applied in metal processing equipment, devices for coating liquid on the surface, manufacturing tools, etc., can solve the problems of low efficiency of painting equipment, reduced processing quality, low processing efficiency, etc., and achieve improved grinding Work efficiency and processing quality, improvement of painting efficiency and uniformity, effect of improving painting efficiency
- Summary
- Abstract
- Description
- Claims
- Application Information
AI Technical Summary
Problems solved by technology
Method used
Image
Examples
Embodiment Construction
[0026] Such as Figure 2-7 As shown, the intake cylinder head processing device includes an automatic sanding machine device and a paint spraying machine connected in sequence, for processing such as figure 1 The surface of the shown air intake cylinder head 6' is polished and painted. The automatic sander device includes an abrasive belt 1, a frame 2, a driving wheel 3 and a driven wheel 4 cooperating with the driving wheel 3. The driving wheel 3 and The driven wheel 4 is horizontally arranged on the frame 2, the abrasive belt 1 is wrapped around the outer edge of the driving wheel 3 and the driven wheel 4, and two sets of retaining plates 5 are horizontally arranged above the abrasive belt 1, so that The two ends of the material blocking plate 5 are fixed on the frame 2 on both sides of the abrasive belt 1 through telescopic brackets 6, and there is a gap between the bottom end of the material blocking plate 5 and the upper surface of the abrasive belt 1.
[0027] In order ...
PUM
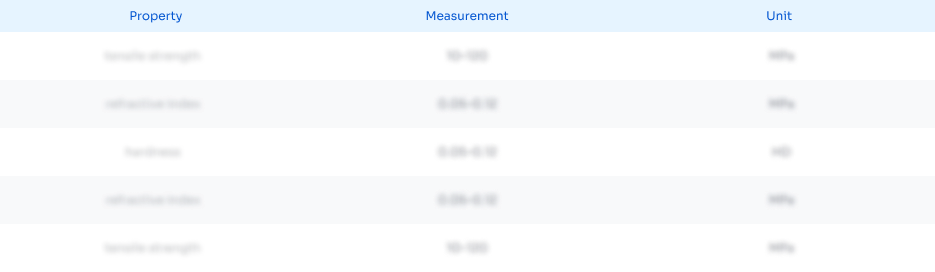
Abstract
Description
Claims
Application Information

- Generate Ideas
- Intellectual Property
- Life Sciences
- Materials
- Tech Scout
- Unparalleled Data Quality
- Higher Quality Content
- 60% Fewer Hallucinations
Browse by: Latest US Patents, China's latest patents, Technical Efficacy Thesaurus, Application Domain, Technology Topic, Popular Technical Reports.
© 2025 PatSnap. All rights reserved.Legal|Privacy policy|Modern Slavery Act Transparency Statement|Sitemap|About US| Contact US: help@patsnap.com