Recycling and Utilization of Tailing Slag from Vanadium Extraction by Calcium Method
A technology for extracting vanadium tailings and calcium method, which is applied in the solid-liquid separation process, recycling of calcium method for vanadium extraction tailings, and mineral processing, and can solve the problems of difficult-to-return sintering applications and high sulfur content in calcium-based vanadium extraction tailings. Achieve efficient utilization, reduce sulfur content, and reduce costs
- Summary
- Abstract
- Description
- Claims
- Application Information
AI Technical Summary
Problems solved by technology
Method used
Image
Examples
Embodiment 1
[0040] Embodiment 1 Using the technical scheme of the present invention to reclaim the tailings of vanadium extraction by calcium method
[0041] A method for utilizing the tailings of vanadium extraction by calcium method, the specific steps are:
[0042]Weigh 50g of the above-mentioned vanadium extraction tailings by the calcium method and place it in the XFD-1.5 single-cell flotation cell, add 1L of water, stir evenly; add 10ml of alcohol, 3 Stir with air at a rate of 1 / h for 2 minutes, add 0.1 g of sodium oleate, continue stirring for 3 minutes, float until the foam no longer increases, filter and dry the obtained foam and pulp respectively to obtain gypsum and iron-rich materials. The yield of the obtained gypsum is 11.6%, the gypsum contains 13.8% sulfur, and the sulfur yield is 72%; the iron-rich material contains 0.7% sulfur, 34.4% iron, and the iron yield is greater than 90%.
Embodiment 2
[0043] Embodiment 2 Using the technical scheme of the present invention to reclaim the tailings of vanadium extraction by calcium method
[0044] A method for utilizing the tailings of vanadium extraction by calcium method, the specific steps are:
[0045] Weigh 100g of the above-mentioned vanadium extraction tailings by the calcium method and place it in the XFD-1.5 single-trough flotation cell, add 1L of water, stir evenly; add 5ml of water glass, and use 5m 3 Add air at a rate of 1-5min and stir for 1-5min, add 0.1g sodium lauryl sulfate, continue to stir for 5min, float until the foam no longer increases, filter and dry the obtained concentrate foam and tailings slurry respectively to obtain Gypsum and iron-rich materials. The yield of the obtained gypsum is 15.6%, the gypsum contains 12.7% of sulfur, and the sulfur yield is 69%; the iron-rich material contains 1.0% of sulfur, 31.1% of iron, and the iron yield is greater than 88%.
Embodiment 3
[0046] Embodiment 3 Using the technical scheme of the present invention to reclaim the tailings of vanadium extraction by calcium method
[0047] A method for utilizing the tailings of vanadium extraction by calcium method, the specific steps are:
[0048] Weigh 100g of the above-mentioned vanadium extraction tailings by the calcium method and place it in the XFD-1.5 single-cell flotation cell, add 1L of water, and use 2m 3 The speed of / h feeds air and stirs 2min, adjusts pH to 9.0 with sulfuric acid, calcium hydroxide; Add 0.1g sodium dodecylbenzene sulfonate, continue stirring 2min, flotation until foam no longer increases, respectively to the refined The ore foam and tailings slurry are filtered and dried to obtain gypsum and iron-rich materials. The yield of the obtained gypsum is 22.6%, the gypsum contains 16.4% sulfur, and the sulfur yield is 93.9%; the iron-rich material contains 0.3% sulfur, 34.1% iron, and the iron yield is 93.8%.
PUM
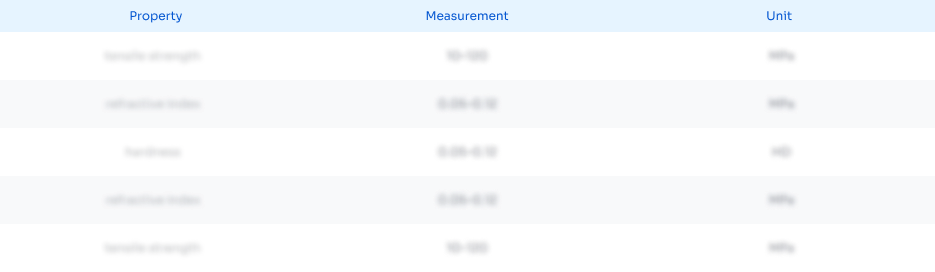
Abstract
Description
Claims
Application Information

- Generate Ideas
- Intellectual Property
- Life Sciences
- Materials
- Tech Scout
- Unparalleled Data Quality
- Higher Quality Content
- 60% Fewer Hallucinations
Browse by: Latest US Patents, China's latest patents, Technical Efficacy Thesaurus, Application Domain, Technology Topic, Popular Technical Reports.
© 2025 PatSnap. All rights reserved.Legal|Privacy policy|Modern Slavery Act Transparency Statement|Sitemap|About US| Contact US: help@patsnap.com