Technique for processing monazite through alkaline method and separating rare earth through extraction
A technology for monazite and rare earth, which is applied in the field of alkaline treatment of monazite, extraction and separation of rare earth, and organic phase loaded with rare earth, can solve problems such as environmental pollution, and achieve the effect of reducing alkali consumption, radioactive pollution and inhibiting harmful problems.
- Summary
- Abstract
- Description
- Claims
- Application Information
AI Technical Summary
Problems solved by technology
Method used
Image
Examples
Embodiment 1
[0043] The REO content is 51.2% monazite (ThO2 content 3.9%) and 40% liquid caustic soda are placed in the reaction kettle of nitrogen protection atmosphere with the liquid-solid ratio of 3:1, adopt far-infrared heating to 140 ℃ decomposition reaction, reaction After the slurry is filtered and washed, the decomposition rate of monazite is 97.9%. Among them, the proportion of cerium Ce3+ / ΣCe in the form of +3 valence cerium hydroxide in the rare earth hydroxide is 89%. The lye in the filtrate is recovered and recycled, and the ton ore consumption Sodium hydroxide 0.57 tons.
[0044] Dissolve the rare earth hydroxide alkali cake with 0.2mol / L P204 at 20°C, no chlorine gas is generated on site during the process of dissolving the above filter cake, and an organic phase with a loaded rare earth concentration of 0.02mol / L is obtained, and the extraction yield of rare earth It reaches 99.1%, the extraction yield of thorium is 0.035%, and the separation of thorium and rare earth is r...
Embodiment 2
[0047] Put monazite with REO content of 31.1% (ThO2 content 3.1%) and 65% liquid caustic soda at a liquid-solid ratio of 1.5:1 in a reaction kettle with an argon protective atmosphere, and use eddy current electric heating to 80°C for decomposition and reaction , the reaction slurry is filtered and washed, and the monazite decomposition rate is 96.5%, wherein the cerium ratio Ce3+ / ΣCe existing in the form of +3 valence cerium hydroxide in the rare earth hydroxide is 95%, and the lye is recovered and recycled in the filtrate, tons The mine consumes 0.42 tons of sodium hydroxide.
[0048] Dissolve the rare earth hydroxide alkali cake with 0.5mol / L C272 at 50°C, no chlorine gas is generated on site during the process of dissolving the above filter cake, and an organic phase with a loaded rare earth concentration of 0.05mol / L is obtained, and the extraction yield of rare earth It reaches 99.0%, the extraction yield of thorium is less than 0.01%, and the separation of thorium and r...
Embodiment 3
[0051] Put REO content of 64.9% monazite (ThO2 content of 4.3%) and 20% liquid caustic soda at a liquid-solid ratio of 10:1 in a tubular reactor with a helium protective atmosphere, and use steam to heat to 345°C for decomposition reaction Finally, the reaction slurry is filtered and washed, and the monazite decomposition rate is 98.5%, wherein the cerium ratio Ce3+ / ΣCe in the form of +3 valence cerium hydroxide in the rare earth hydroxide is 85%, and the lye in the filtrate is recovered and recycled. Ton of ore consumes 0.71 tons of sodium hydroxide.
[0052] Dissolve the rare earth hydroxide alkali cake with 0.9mol / L naphthenic acid at 30°C, no chlorine gas is generated on site during the process of dissolving the above filter cake, and an organic phase with a loaded rare earth concentration of 0.09mol / L is obtained, and the extraction yield of the rare earth is The extraction rate reaches 92.5%, the extraction yield of thorium is 0.014%, and the separation of thorium and ra...
PUM
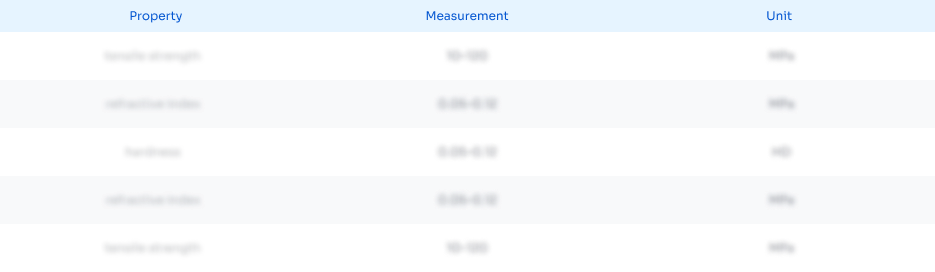
Abstract
Description
Claims
Application Information

- Generate Ideas
- Intellectual Property
- Life Sciences
- Materials
- Tech Scout
- Unparalleled Data Quality
- Higher Quality Content
- 60% Fewer Hallucinations
Browse by: Latest US Patents, China's latest patents, Technical Efficacy Thesaurus, Application Domain, Technology Topic, Popular Technical Reports.
© 2025 PatSnap. All rights reserved.Legal|Privacy policy|Modern Slavery Act Transparency Statement|Sitemap|About US| Contact US: help@patsnap.com