A kind of dephosphorization method of converter with oxygen tapping
A converter and converter smelting technology, applied in the field of metallurgy, can solve the problems of large temperature drop of dephosphorization hot metal, increased steelmaking cost, small reaction interface, etc., and achieve the effects of improving dephosphorization efficiency, low cost and improving dephosphorization effect.
- Summary
- Abstract
- Description
- Claims
- Application Information
AI Technical Summary
Problems solved by technology
Method used
Examples
Embodiment 1
[0035] The dephosphorization of the converter ladle adopts the following specific process steps.
[0036] 100 tons of converter conventional smelting; converter end point [C] 0.035%, [O] 650ppm, [P] content 0.015%, molten iron temperature [T] 1705 ℃. The weight ratio of the slag components at the end of the converter: CaO 55%, MgO 12%, SiO 2 17%, Al 2 o 3 1%, FeO 15%.
[0037] The converter is tapped with oxygen. When tapping 30%, add lime 2kg / ton steel, fluorite 0.2kg / ton steel, and add modifier 0.8kg / ton steel after tapping. After the steel tapping is completed, the strong stirring gas volume is 12L / min, and the ladle is dephosphorized by stirring for 3 minutes; the mass composition of the modifier is: CaO 20%, MgO 5%, SiO 2 5%, Al 2 o 3 20%, Al 50%.
[0038] The composition of ladle slag after tapping is 40% CaO, 6% MgO, SiO 2 12%, Al 2 o 3 37%, FeO 5%.
[0039] After the ladle is dephosphorized, the [P] content is reduced from 0.015% to 0.011%.
Embodiment 2
[0041] The method for suppressing slag in the converter adopts the following specific process steps.
[0042] 100 tons of converter conventional smelting; converter end point [C] 0.035%, [O] 600ppm, [P] content 0.015%, molten iron temperature [T] 1685 ℃. The weight ratio of the slag components at the end of the converter: CaO 51%, MgO 8%, SiO 2 17%, Al 2 o 3 3%, FeO 21%.
[0043] The converter is tapped with oxygen. When tapping 50%, add lime 4kg / ton steel, fluorite 0.4kg / ton steel, add modifier 0.8kg / ton steel after tapping, strong stirring gas volume 10L / min after tapping, Stir for 3 minutes for ladle dephosphorization. The mass composition of the modifier is: CaO 30%, MgO 2%, SiO 2 3%, Al 2 o 3 20%, Al 45%.
[0044] The composition of ladle slag after tapping is 30% CaO, 12% MgO, SiO 2 7%, Al 2 o 3 40%, FeO 11%.
[0045] After the ladle is dephosphorized, the [P] content is reduced from 0.015% to 0.009%.
Embodiment 3
[0047] The method for suppressing slag in the converter adopts the following specific process steps.
[0048] Conventional smelting in a 100-ton converter; converter endpoint [C] 0.035%, [O] 600ppm, [P] content 0.013%, molten iron temperature [T] 1685°C. The weight ratio of the slag components at the end of the converter: CaO 45%, MgO 12%, SiO 2 17%, Al 2 o 3 5%, FeO 21%.
[0049] When tapping 30% of the steel in the converter, add lime 4kg / ton steel and fluorite 0.4kg / ton steel, add modifier 1.2kg / ton steel when tapping 80% of the steel, and after the steel tapping is completed, the strong stirring gas volume is 8L / min , stirring for 3 minutes for ladle dephosphorization. The mass composition of the modifier is: CaO 25%, MgO 3%, SiO 2 2%, Al 2 o 3 20%, Al 50%.
[0050] The composition of ladle slag after tapping is 40% CaO, 10% MgO, SiO 2 6%, Al 2 o 3 35%, FeO 9%.
[0051] After the ladle is dephosphorized, the [P] content is reduced from 0.013% to 0.009%....
PUM
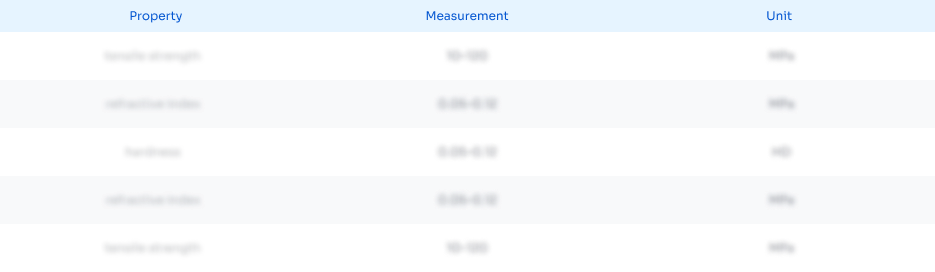
Abstract
Description
Claims
Application Information

- Generate Ideas
- Intellectual Property
- Life Sciences
- Materials
- Tech Scout
- Unparalleled Data Quality
- Higher Quality Content
- 60% Fewer Hallucinations
Browse by: Latest US Patents, China's latest patents, Technical Efficacy Thesaurus, Application Domain, Technology Topic, Popular Technical Reports.
© 2025 PatSnap. All rights reserved.Legal|Privacy policy|Modern Slavery Act Transparency Statement|Sitemap|About US| Contact US: help@patsnap.com