Hydrolysis-resistant artificial leather and preparation method thereof
A hydrolysis-resistant, artificial leather technology, applied in the field of artificial leather, can solve the problem of easy falling off on the surface, and achieve the effects of not easy to fall off, effective water resistance, and convenient operation.
- Summary
- Abstract
- Description
- Claims
- Application Information
AI Technical Summary
Problems solved by technology
Method used
Examples
preparation example Construction
[0017] The present invention also provides a method for preparing hydrolysis-resistant artificial leather. According to the ratio of the raw materials of the surface layer, middle layer and foam layer in the above-mentioned hydrolysis-resistant artificial leather, the surface layer slurry, the middle layer slurry and the foaming layer are prepared respectively. layer slurry, then coat the surface layer slurry on the release paper, and dry at 100-150°C for 50-60S; coat the middle layer slurry on the dried surface layer slurry, And dry at 150-170°C for 75-90S; apply the foam layer slurry on the dried middle layer slurry, and foam at 170-190°C; then apply the adhesive Coat on the fully foamed foam layer slurry, then stick the artificial leather base cloth on the foam layer slurry coated with adhesive, and dry at 120-160°C for 120-140S ; Then the release paper is peeled off to obtain the hydrolysis-resistant artificial leather.
[0018] As can be seen from the foregoing descripti...
Embodiment 1
[0035]A hydrolysis-resistant artificial leather comprises a surface layer, a middle layer, a foam layer, an adhesive layer and an artificial leather base cloth arranged in sequence, and the foam layer is adhered to the artificial leather base cloth through the adhesive layer. The surface layer is prepared from the following raw materials in parts by weight: 95 parts of WR-1060 type hydrolysis-resistant resin, 50 parts of organic solvent, 5 parts of polyether additives with hydrolysis resistance and 3 parts of PU color paste. The decomposed resin is polyether or polyether compounds; the intermediate layer is prepared from the following raw materials in parts by weight: 95 parts of polyvinyl chloride resin, 60 parts of diisononyl phthalate, 4 parts of PVC color paste and 1 BaZn in parts by weight; the foam layer is prepared from the following raw materials in parts by weight: 95 parts of polyvinyl chloride resin, 75 parts of diisononyl phthalate, 50 parts of filler, 3 parts of PV...
Embodiment 2
[0038] A hydrolysis-resistant artificial leather comprises a surface layer, a middle layer, a foam layer, an adhesive layer and an artificial leather base cloth arranged in sequence, and the foam layer is adhered to the artificial leather base cloth through the adhesive layer. The surface layer is prepared from the following raw materials in parts by weight: 105 parts of WR-1060 type hydrolysis-resistant resin, 70 parts of organic solvent, 10 parts of polyether additives with hydrolysis resistance and 7 parts of PU color paste. The decomposed resin is polyether or polyether compounds; the intermediate layer is prepared from the following raw materials in parts by weight: 105 parts of polyvinyl chloride resin, 70 parts of diisononyl phthalate, 7 parts of PVC color paste and 2 BaZn in parts by weight; the foam layer is prepared from the following raw materials in parts by weight: 105 parts of polyvinyl chloride resin, 85 parts of diisononyl phthalate, 70 parts of filler, 5 parts ...
PUM
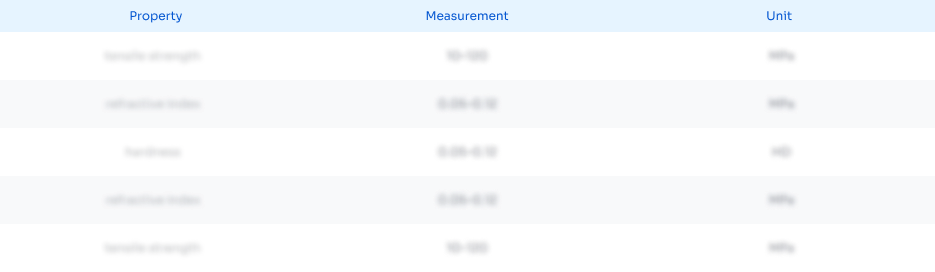
Abstract
Description
Claims
Application Information

- R&D Engineer
- R&D Manager
- IP Professional
- Industry Leading Data Capabilities
- Powerful AI technology
- Patent DNA Extraction
Browse by: Latest US Patents, China's latest patents, Technical Efficacy Thesaurus, Application Domain, Technology Topic, Popular Technical Reports.
© 2024 PatSnap. All rights reserved.Legal|Privacy policy|Modern Slavery Act Transparency Statement|Sitemap|About US| Contact US: help@patsnap.com