Preparing method of 3D-structuer Ni/rGO composite hydrogen evolution electrode
A hydrogen evolution electrode, 3D technology, applied in electrodes, electrode shapes/types, electrolytic coatings, etc., can solve problems such as hindering metal ions, coating micropores, microcracks, reducing graphene content in composite coatings, etc., to enhance the bonding ability. , Increase the specific surface area, the effect of stable performance
- Summary
- Abstract
- Description
- Claims
- Application Information
AI Technical Summary
Problems solved by technology
Method used
Image
Examples
Embodiment 1
[0028] (1) Pretreatment of substrate
[0029] Before electrodeposition, immerse the foam nickel substrate in a container filled with deionized water, and ultrasonically treat it for 5 minutes; then put the foam nickel into 3M HCl solution for acidification treatment for 30 seconds, then wash it with deionized water until it is neutral, and dry it for later use;
[0030] (2) Preparation of graphene oxide dispersion
[0031] Adopt improved Hummers method to prepare graphite oxide, add the graphite oxide of 1.0g to 1L deionized water, process 2h with the ultrasonic power of 150W, obtain the homogeneous, brown graphene oxide dispersion liquid that concentration is 1.0g / L;
[0032] (3) Preparation of composite plating solution
[0033] Add nickel sulfamate 350g, nickel chloride 10g, ammonium chloride 30g in the graphene oxide dispersion liquid prepared in step (2), process 2h with the ultrasonic power of 150W, finally obtain uniform, dark green composite plating solution, The pH ...
Embodiment 2
[0039] (1) Pretreatment of substrate
[0040] Before electrodeposition, immerse the foam nickel substrate in a container filled with deionized water, and ultrasonically treat it for 5 minutes; then put the foam nickel into 3M HCl solution for acidification treatment for 30 seconds, then wash it with deionized water until it is neutral, and dry it for later use;
[0041] (2) Preparation of graphene oxide dispersion
[0042] Adopt improved Hummers method to prepare graphite oxide, add the graphite oxide of 0.1g to 1L deionized water, process 1h with the ultrasonic power of 100W, obtain the homogeneous, brown graphene oxide dispersion liquid that concentration is 0.1g / L;
[0043] (3) Preparation of composite plating solution
[0044] Add nickel sulfamate 350g, nickel chloride 10g, ammonium chloride 30g in the graphene oxide dispersion liquid prepared in step (2), process 1h with the ultrasonic power of 100W, finally obtain uniform, dark green composite plating solution, The pH ...
Embodiment 3
[0050] (1) Pretreatment of substrate
[0051] Before electrodeposition, immerse the foam nickel substrate in a container filled with deionized water, and ultrasonically treat it for 5 minutes; then put the foam nickel into 3M HCl solution for acidification treatment for 30 seconds, then wash it with deionized water until it is neutral, and dry it for later use;
[0052] (2) Preparation of graphene oxide dispersion
[0053] Adopt improved Hummers method to prepare graphite oxide, add the graphite oxide of 1.5g to 1L deionized water, process 3h with the ultrasonic power of 150W, obtain the homogeneous, brown graphene oxide dispersion liquid that concentration is 1.5g / L;
[0054] (3) Preparation of composite plating solution
[0055] Add nickel sulfamate 350g, nickel chloride 10g, ammonium chloride 30g in the graphene oxide dispersion prepared in step (2), process 3h with the ultrasonic power of 150W, finally obtain uniform, dark green composite plating solution, The pH value o...
PUM
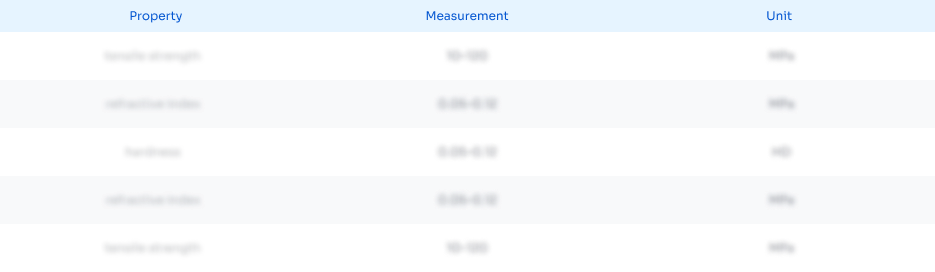
Abstract
Description
Claims
Application Information

- R&D
- Intellectual Property
- Life Sciences
- Materials
- Tech Scout
- Unparalleled Data Quality
- Higher Quality Content
- 60% Fewer Hallucinations
Browse by: Latest US Patents, China's latest patents, Technical Efficacy Thesaurus, Application Domain, Technology Topic, Popular Technical Reports.
© 2025 PatSnap. All rights reserved.Legal|Privacy policy|Modern Slavery Act Transparency Statement|Sitemap|About US| Contact US: help@patsnap.com