Dyeing and laminating process for glass fiber reinforced plastics
A fiberglass and film-coating technology, which is applied in the field of glass fiber reinforced plastic dyeing and film-coating technology, can solve the problems of material loss, uneven paint and coating, cumbersome processing steps, etc., and achieve the effects of reducing labor intensity, improving work efficiency, and reducing labor intensity
- Summary
- Abstract
- Description
- Claims
- Application Information
AI Technical Summary
Problems solved by technology
Method used
Examples
Embodiment Construction
[0015] In order to make the technical means, creative features, goals and effects achieved by the present invention easy to understand, the present invention will be further elaborated below in conjunction with specific embodiments, but the following embodiments are only preferred embodiments of the present invention, not all. Based on the examples in the implementation manners, other examples obtained by those skilled in the art without making creative efforts all belong to the protection scope of this patent.
[0016] A kind of glass fiber reinforced plastic dyeing coating process comprises the following steps:
[0017] 1) Dyeing premix: add air-dry gel coat with a mass ratio of 18%-20% to the resin as a dyeing agent for premixing.
[0018] 2) Adding curing agent and stirring: add curing agent with a mass ratio of 0.8%-1.5% to the pre-mixed resin, and then fully stir through the mixing drum at a stirring speed of 1000r / min and a stirring temperature of 25°C to finally obtain...
PUM
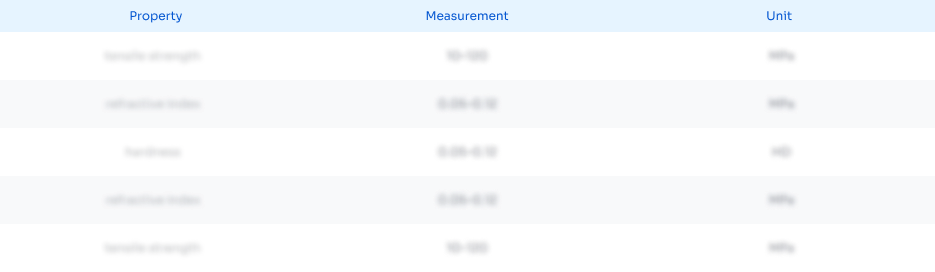
Abstract
Description
Claims
Application Information

- Generate Ideas
- Intellectual Property
- Life Sciences
- Materials
- Tech Scout
- Unparalleled Data Quality
- Higher Quality Content
- 60% Fewer Hallucinations
Browse by: Latest US Patents, China's latest patents, Technical Efficacy Thesaurus, Application Domain, Technology Topic, Popular Technical Reports.
© 2025 PatSnap. All rights reserved.Legal|Privacy policy|Modern Slavery Act Transparency Statement|Sitemap|About US| Contact US: help@patsnap.com