Precoated sand regenerating production line
A production line and technology of coated sand, applied in the field of iron and steel casting, can solve the problems of wasting natural resources and polluting the environment by the waste of coated sand, and achieve the effect of reducing production costs and reducing environmental pollution
- Summary
- Abstract
- Description
- Claims
- Application Information
AI Technical Summary
Problems solved by technology
Method used
Image
Examples
Embodiment Construction
[0009] In order to further illustrate the technical solution of the present invention, the specific implementation of the present invention is now described in conjunction with the accompanying drawings. According to the scale of coated sand casting, the production capacity of the coated sand regeneration production line is selected, that is, the amount of coated sand waste processed per unit time , so as not to cause waste of production capacity or the phenomenon of not being able to meet production needs; select commercially available pulverizers and screening machines in this industry as raw material pulverizers and raw material screening machines 1, and install them on the feed port side of the raw material conveyor 2 ; Select the commercially available general belt conveyor in this industry as the raw material conveyor 2 in this example, and install it on the discharge port one end of the raw material pulverizer and the raw material screening machine 1, and connect its disc...
PUM
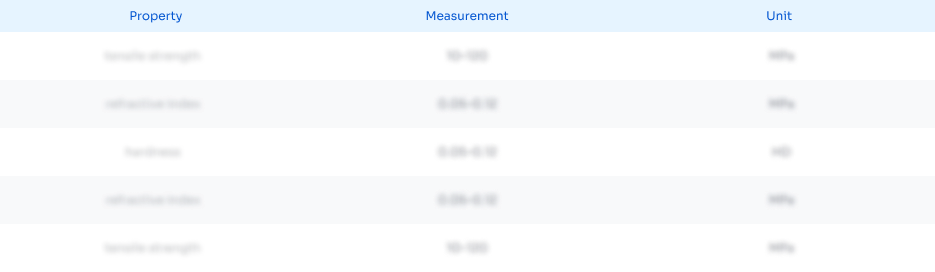
Abstract
Description
Claims
Application Information

- R&D Engineer
- R&D Manager
- IP Professional
- Industry Leading Data Capabilities
- Powerful AI technology
- Patent DNA Extraction
Browse by: Latest US Patents, China's latest patents, Technical Efficacy Thesaurus, Application Domain, Technology Topic, Popular Technical Reports.
© 2024 PatSnap. All rights reserved.Legal|Privacy policy|Modern Slavery Act Transparency Statement|Sitemap|About US| Contact US: help@patsnap.com