Electromechanical rotational damper with tension and compression stop
A technology of rotating shock absorbers and shock absorbers, applied in non-rotating vibration suppression, springs/shock absorbers, mechanical equipment, etc.
- Summary
- Abstract
- Description
- Claims
- Application Information
AI Technical Summary
Problems solved by technology
Method used
Image
Examples
Embodiment Construction
[0023] figure 1 A side view of a torsional vibration damper 2 is shown, which has a damper housing 4 fastened to a mass, the wheel suspension, by fasteners (not shown) or on the vehicle body. The articulated rod 6 is mounted pivotably relative to the shock absorber housing 4 and is connected to a second mass, ie the vehicle body or the wheel suspension. The articulated rod 6 is connected to a housing cover 8 , which is rotatably mounted on the shock absorber housing 4 . A harmonic drive 10 is arranged between the damper housing 4 and the housing cover 8 .
[0024] figure 2 showing along figure 1 The II-II line in the section cuts the sectional view of the rotary vibration absorber. The torsional vibration damper 2 here comprises a harmonic drive comprising a rigid unit 12 with internal toothing connected to the damper housing 4 and a rigid unit 12 with external toothing connected to the housing cover 8 . The connected flexible unit 14 is described below. The two units ...
PUM
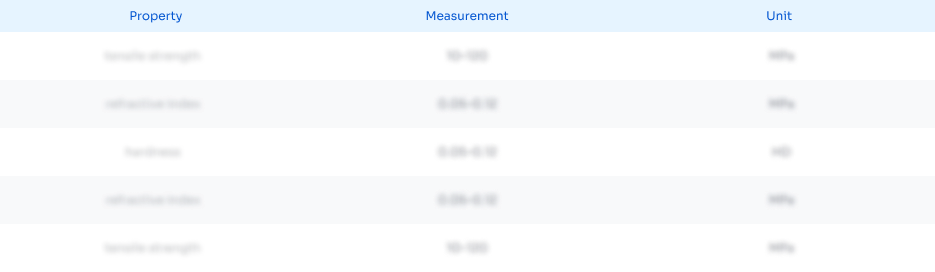
Abstract
Description
Claims
Application Information

- R&D
- Intellectual Property
- Life Sciences
- Materials
- Tech Scout
- Unparalleled Data Quality
- Higher Quality Content
- 60% Fewer Hallucinations
Browse by: Latest US Patents, China's latest patents, Technical Efficacy Thesaurus, Application Domain, Technology Topic, Popular Technical Reports.
© 2025 PatSnap. All rights reserved.Legal|Privacy policy|Modern Slavery Act Transparency Statement|Sitemap|About US| Contact US: help@patsnap.com