A kind of sheath type magnesium oxide for fireproof cable
A technology of fireproof cable and fused magnesia, applied in the field of magnesia, can solve the problems of non-moisture resistance, low insulation, temperature difference resistance, etc., and achieve the effect of improving insulation performance, reducing production cost, and formulating scientifically.
- Summary
- Abstract
- Description
- Claims
- Application Information
AI Technical Summary
Problems solved by technology
Method used
Image
Examples
Embodiment 1
[0034] This embodiment discloses a preparation method of sheathed magnesium oxide for fireproof cables, comprising the following steps:
[0035] Step 1. The fused magnesia raw material is pulverized to 300-400 mesh, magnetically separated by a magnetic separator to remove ferromagnetic impurities, then baked in a rotary furnace at 600°C, and cooled for later use;
[0036] Step 2, calcining kaolin with an iron oxide content lower than 0.4 at a temperature of 800° C. for 1 hour;
[0037] Step 3, silicone oil and toluene are configured into a solution according to the weight ratio of 1:90;
[0038] Step 4, mixing the fused magnesia obtained in step 1 with the kaolin obtained in step 2 in a blender at a weight ratio of 1000:4;
[0039] Step 5. Mix the mixture obtained in step 4 with the solution prepared in step 3 in a blender at a weight ratio of 1000:1;
[0040] Step 6, drying the mixture obtained in step 5 in a rotary oven at 300°C for 60 minutes, and cooling it for use;
[...
Embodiment 2
[0050] This embodiment discloses a preparation method of sheathed magnesium oxide for fireproof cables, comprising the following steps:
[0051] Step 1. The fused magnesia raw material is pulverized to 200-300 mesh, magnetically separated by a magnetic separator to remove ferromagnetic impurities, then baked in a rotary furnace at 700°C, and cooled for later use;
[0052] Step 2, calcining kaolin with an iron oxide content lower than 0.5 at a temperature of 900° C. for 3 hours;
[0053] Step 3, silicone oil and toluene are configured into a solution according to the weight ratio of 1:90;
[0054] Step 4, mixing the fused magnesia obtained in step 1 with the kaolin obtained in step 2 in a blender at a weight ratio of 1000:5;
[0055] Step 5. Mix the mixture obtained in step 4 with the solution prepared in step 3 in a blender at a weight ratio of 1100:1;
[0056] Step 6, drying the mixture obtained in step 5 in a rotary oven at 400°C for 30 minutes, and cooling it for use;
...
Embodiment 3
[0066] This embodiment discloses a preparation method of sheathed magnesium oxide for fireproof cables, comprising the following steps:
[0067] Step 1. The fused magnesia raw material is pulverized to 400-500 mesh, magnetically separated by a magnetic separator to remove ferromagnetic impurities, then baked in a rotary furnace at 500-700°C, and cooled for later use;
[0068] Step 2, calcining kaolin with an iron oxide content lower than 0.5 at a temperature of 900° C. for 3 hours;
[0069] Step 3, silicone oil and toluene are configured into a solution according to the weight ratio of 1:120;
[0070] Step 4, mixing the fused magnesia obtained in step 1 with the kaolin obtained in step 2 in a blender at a weight ratio of 1000:7;
[0071] Step 5. Mix the mixture obtained in step 4 with the solution prepared in step 3 in a blender at a weight ratio of 900:1;
[0072] Step 6, drying the mixture obtained in step 5 in a rotary oven at 200°C for 90 minutes, and cooling it for use;...
PUM
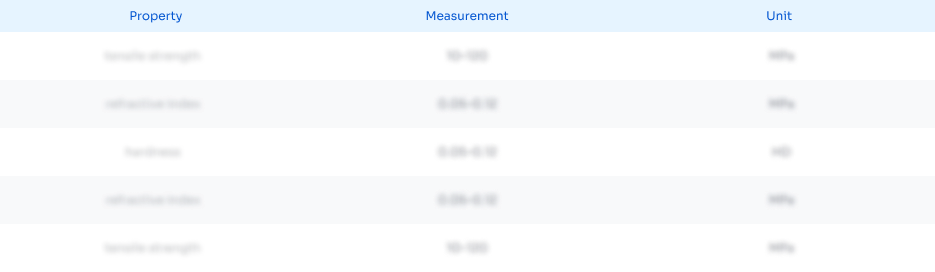
Abstract
Description
Claims
Application Information

- R&D Engineer
- R&D Manager
- IP Professional
- Industry Leading Data Capabilities
- Powerful AI technology
- Patent DNA Extraction
Browse by: Latest US Patents, China's latest patents, Technical Efficacy Thesaurus, Application Domain, Technology Topic, Popular Technical Reports.
© 2024 PatSnap. All rights reserved.Legal|Privacy policy|Modern Slavery Act Transparency Statement|Sitemap|About US| Contact US: help@patsnap.com