Partial Repair Method of Rotary Kiln Lining
A technology of rotary kiln and kiln lining, which is applied in the direction of lining repair, furnace, lighting and heating equipment, etc. It can solve the problems of short service life, refractory brick falling off, high working hours, etc., achieve rapid and effective repair, prolong service life and save time and cost effects
- Summary
- Abstract
- Description
- Claims
- Application Information
AI Technical Summary
Problems solved by technology
Method used
Image
Examples
Embodiment 1
[0026] Embodiment 1: The partial repair method of the kiln lining of this rotary kiln adopts the following specific process.
[0027] The above process is adopted, wherein: the mixing ratio of dry material and water in the pouring material is 100:6 mass ratio, and the mixing time is 15 minutes; after standing for 2.5 hours, clean water is used for health preservation, and then water is used for health preservation again every 4 hours, and the health preservation is performed twice in total. After the repair is completed, the use effect is good, and the service life of the rotary kiln is extended by 8 to 12 months.
Embodiment 2
[0028] Embodiment 2: The partial repair method of the kiln lining of this rotary kiln adopts the following specific process.
[0029] The above process is adopted, wherein: the mixing ratio of dry material and water in the pouring material is 100:5 by mass, and the mixing time is 10 minutes; after standing for 2 hours, clean water is used for health preservation, and then water is used for health preservation again every 5 hours, for a total of 2 times of health preservation. After the repair is completed, the service life of the rotary kiln is extended by 4 to 6 months.
Embodiment 3
[0030] Embodiment 3: The partial repair method of the kiln lining of this rotary kiln adopts the following specific process.
[0031] The above process is adopted, wherein: the mixing ratio of dry material and water in the pouring material is 100:7 mass ratio, and the mixing time is 20 minutes; after standing for 4 hours, clean water is used for health preservation, and then water is used for health preservation again every 3 hours, and a total of 3 times of health preservation. After the repair is completed, the service life of the rotary kiln will be extended by 6 to 8 months.
PUM
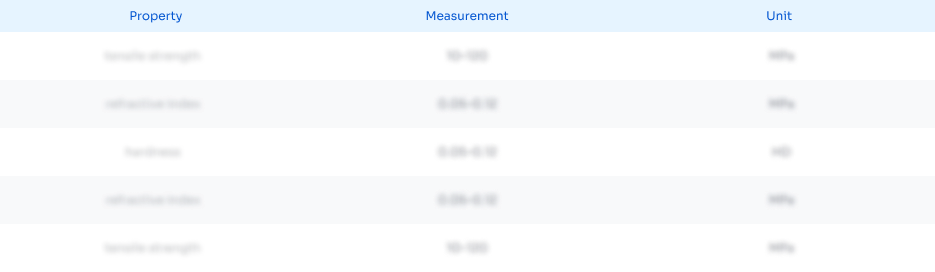
Abstract
Description
Claims
Application Information

- R&D Engineer
- R&D Manager
- IP Professional
- Industry Leading Data Capabilities
- Powerful AI technology
- Patent DNA Extraction
Browse by: Latest US Patents, China's latest patents, Technical Efficacy Thesaurus, Application Domain, Technology Topic, Popular Technical Reports.
© 2024 PatSnap. All rights reserved.Legal|Privacy policy|Modern Slavery Act Transparency Statement|Sitemap|About US| Contact US: help@patsnap.com