An external reinforcement system for 3D printed cores
A 3D printing and core technology, which is applied in the direction of cores, molds, mold components, etc., can solve the problems of shortening the printing cycle, increasing production costs, and insufficient core strength, etc., and achieves the improvement of porosity defects and the reduction of production costs , Improve the effect of external strength
- Summary
- Abstract
- Description
- Claims
- Application Information
AI Technical Summary
Problems solved by technology
Method used
Image
Examples
Embodiment Construction
[0024] In order to enable those skilled in the art to better understand the technical solutions of the present invention, the present invention will be further described in detail below in conjunction with specific examples. The embodiments described below are exemplary only for explaining the present invention and should not be construed as limiting the present invention. If no specific technique or condition is indicated in the examples, it shall be carried out according to the technique or condition described in the literature in this field or according to the product specification.
[0025] The present invention provides an external reinforcement system for a 3D printing core. According to an embodiment of the present invention, figure 1 is a schematic diagram of the structure of the double-layer sand box, figure 2 is the sectional view of the bottom plate, image 3 is the structural diagram of the negative pressure system, refer to figure 1 , figure 2 with image 3...
PUM
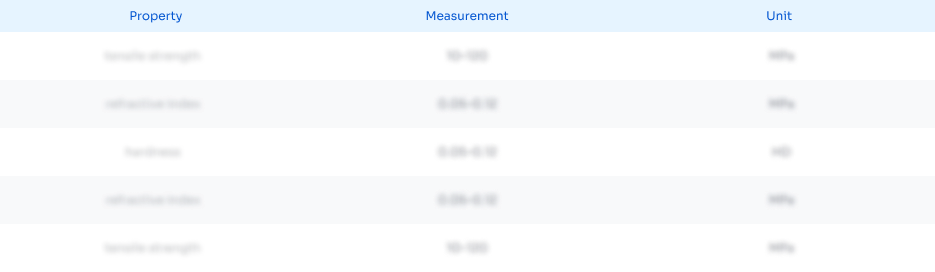
Abstract
Description
Claims
Application Information

- Generate Ideas
- Intellectual Property
- Life Sciences
- Materials
- Tech Scout
- Unparalleled Data Quality
- Higher Quality Content
- 60% Fewer Hallucinations
Browse by: Latest US Patents, China's latest patents, Technical Efficacy Thesaurus, Application Domain, Technology Topic, Popular Technical Reports.
© 2025 PatSnap. All rights reserved.Legal|Privacy policy|Modern Slavery Act Transparency Statement|Sitemap|About US| Contact US: help@patsnap.com