Coke oven gas purification system and condensate treatment subsystem thereof
A technology of processing subsystem and purification system, applied in the field of coke oven gas purification system and its condensate processing subsystem, can solve the problems of long static time, poor separation effect, huge equipment, etc., and achieves short separation time and small footprint , The effect of convenient operation and maintenance
- Summary
- Abstract
- Description
- Claims
- Application Information
AI Technical Summary
Problems solved by technology
Method used
Image
Examples
Embodiment Construction
[0029] In order to make the objectives, technical solutions, and advantages of the embodiments of the present invention clearer, the technical solutions in the embodiments of the present invention will be described clearly and completely in conjunction with the accompanying drawings in the embodiments of the present invention. Obviously, the described embodiments It is a part of the embodiments of the present invention, but not all the embodiments. Based on the embodiments of the present invention, all other embodiments obtained by those of ordinary skill in the art without creative work shall fall within the protection scope of the present invention.
[0030] Such as figure 1 As shown, figure 1 It is a schematic diagram of the working principle of the coke oven gas purification system provided by an embodiment of the present invention.
[0031] The present invention provides a condensate processing subsystem of a coke oven gas purification system, which includes a mechanized cla...
PUM
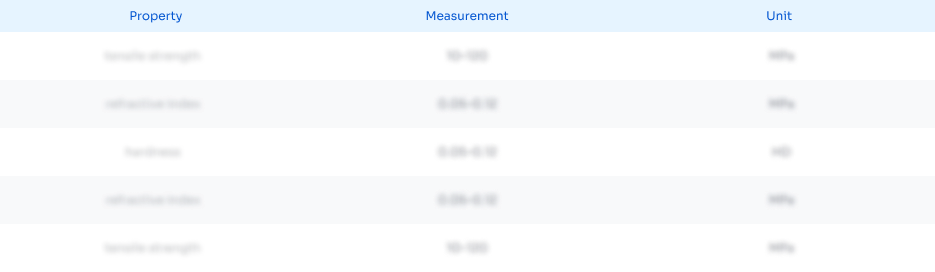
Abstract
Description
Claims
Application Information

- R&D
- Intellectual Property
- Life Sciences
- Materials
- Tech Scout
- Unparalleled Data Quality
- Higher Quality Content
- 60% Fewer Hallucinations
Browse by: Latest US Patents, China's latest patents, Technical Efficacy Thesaurus, Application Domain, Technology Topic, Popular Technical Reports.
© 2025 PatSnap. All rights reserved.Legal|Privacy policy|Modern Slavery Act Transparency Statement|Sitemap|About US| Contact US: help@patsnap.com