Preparation method of slow-rebound polyurethane foam
A polyurethane and slow-rebound technology, applied in the field of polyurethane foam, can solve the problems of lack of slow-rebound polyurethane foam, product technology disclosure, etc., and achieve the effects of eliminating crystallinity, increasing clutter, and good softness
- Summary
- Abstract
- Description
- Claims
- Application Information
AI Technical Summary
Problems solved by technology
Method used
Examples
preparation example Construction
[0024] The invention provides a kind of preparation method of slow resilience polyurethane foam, it comprises the following steps:
[0025] (I) Heat AA and DEG for esterification and polycondensation reaction until the acid value is 20~25mgKOH / g;
[0026] (II) Add oxidized carbon black containing carboxyl and hydroxyl functional groups to the product of step (I), vacuumize, react until the acid value is ≤ 2.0mgKOH / g, increase the vacuum to continue the reaction to obtain modified oxidized carbon black, hydroxyl Ending DEG polyols, i.e. modified DEG polyols;
[0027] (Ⅲ) Add chain extender, catalyst, H to the product obtained in step (II) 2 O, polyether trihydric alcohol, mix as the A component of polyurethane foam after mixing;
[0028] (Ⅳ) After thermal polymerization of diisocyanate and polyether triol, it is used as component B for the preparation of polyurethane foam, wherein the diisocyanate is excessive;
[0029] (Ⅴ) After mixing component A and component B of polyure...
Embodiment 1
[0035] (I) React AA1461.4g with DEG 1226.1g (the amount of DEG added is 0.839 times the amount of AA added by weight) at 210°C for 5h, until the acid value is 25mgKOH / g;
[0036] (II) Add 26.87g (1wt%) of ozone-oxidized carbon black to the product of step (I) to continue the reaction for 4 hours, and vacuumize to remove the water produced by the reaction until the acid value is less than or equal to 2.0mgKOH / g , increase the vacuum until the acid value reaches 0.5mgKOH / g, and the hydroxyl value reaches 35mgKOH / g, so as to obtain DEG polyols modified by oxidized carbon black and terminated by hydroxyl groups, that is, modified DEG polyols;
[0037] (Ⅲ) 500g modified DEG polyol, 100g polyether triol (molecular weight 550), chain extender ethylene glycol 9g (1.5wt%), deionized water 4.8g (0.8wt%), catalyst caprylic acid Bismuth 0.0282g, catalyst triethyldiamine 0.0318g (the weight ratio of the two catalysts is 47:53) was mixed with a high-speed mixer at room temperature for 1.5h,...
Embodiment 2
[0041] (I) React AA1461.4g with DEG 1237.36g (the amount of DEG added is 0.847 times the amount of AA added by weight) at 210°C for 5h, until the acid value is 24mgKOH / g;
[0042] (II) Add 40.31g (1.5wt%) of carbon black oxidized by strong oxidizing acid to the product of step (I) to continue the reaction for 4 hours, and vacuumize to remove the water produced by the reaction until the acid value is ≤ 2.0mgKOH / g, increase the vacuum until the acid value reaches 0.4mgKOH / g, and the hydroxyl value reaches 34mgKOH / g, to obtain DEG polyols modified by oxidized carbon black and terminated with hydroxyl groups, that is, modified DEG polyols;
[0043] (Ⅲ) 500g modified DEG polyol, 100g polyether triol (molecular weight 600), 7.8g (1.3wt%) chain extender 1,3-propanediol, 3.6g (0.6wt%) deionized water, catalyst 0.0282g of bismuth octadecanoate and 0.0318g of catalyst triethylamine (the weight ratio of the two catalysts is 47:53) were mixed with a high-speed mixer at room temperature fo...
PUM
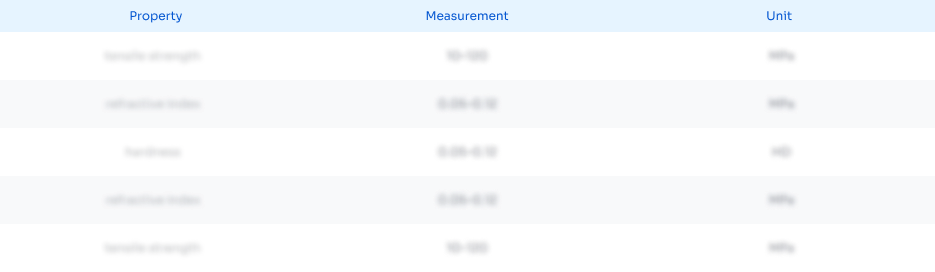
Abstract
Description
Claims
Application Information

- R&D
- Intellectual Property
- Life Sciences
- Materials
- Tech Scout
- Unparalleled Data Quality
- Higher Quality Content
- 60% Fewer Hallucinations
Browse by: Latest US Patents, China's latest patents, Technical Efficacy Thesaurus, Application Domain, Technology Topic, Popular Technical Reports.
© 2025 PatSnap. All rights reserved.Legal|Privacy policy|Modern Slavery Act Transparency Statement|Sitemap|About US| Contact US: help@patsnap.com