A method for manufacturing a wear-resistant layer of a highly wear-resistant chain and a method for manufacturing the wear-resistant sleeve of an oil-free bearing
A production method and wear-resistant layer technology, applied in the field of chains, can solve the problems of restricting the development of high-speed setting machines, increasing the use and maintenance costs of printing and dyeing enterprises, and expensive chain high-temperature grease, so as to improve energy utilization efficiency and eliminate oil pollution. problems, the effect of improving the service life
- Summary
- Abstract
- Description
- Claims
- Application Information
AI Technical Summary
Problems solved by technology
Method used
Image
Examples
Embodiment 1
[0026] Embodiment 1: A high wear-resistant chain, including a chain base 1, a chain 2 hinged with the chain base 1, the two ends of the connecting sleeve 3 of the chain 2 are facing the corresponding connecting holes opened by the chain base 1, and the connecting holes are provided with The shaft pin 4 is inserted into the connecting sleeve 3, and a wear-resistant layer 5 is arranged between the shaft pin 4 and the connecting sleeve 3. The wear-resistant layer 5 includes a base layer 5.1 and a self-lubricating powder layer 5.2 pressed on the base layer 5.1. The base layer 5.1 is 316 Stainless steel wire mesh. The aperture of the 316 stainless steel wire mesh corresponds to the particle diameter of the powder in the self-lubricating powder layer 5.2. The wear-resistant layer 5 is a wear-resistant sheet or a wear-resistant pipe.
Embodiment 2
[0027] Embodiment 2: A high wear-resistant chain, the connecting sleeve 3 is arranged in the oil-free bearing 6, and the oil-free bearing 6 includes the inner oil-free bearing wear-resistant sleeve 6.1 and the outer oil-free bearing outer ring 6.2. The oil-free bearing wear-resistant sleeve 6.1 includes aluminum bronze Al9-4 substrate 6.1.1 and the wear-resistant layer 6.1.2 pressed on the substrate 6.1.1, and the surface of the substrate 6.1.1 is uniformly distributed with prismatic grooves 6.1 around the center of the circle .3.
Embodiment 3
[0028] Embodiment 3: A method for manufacturing a wear-resistant layer of a highly wear-resistant chain, comprising the following steps: preparing self-lubricating powder: by mass percentage: talc powder 10%~30%, PTFE10%~30%, PEEK10%~ 30%, graphite 5%~10%, glass fiber 5%~10%, carbon fiber 5%~10%, and the rest are unavoidable impurities, which are mixed and stirred in order to make a mixed wear-resistant material powder for use; the mixed wear-resistant material The powder is compounded on the 316 stainless steel wire mesh, and combined into one body through heating and repeated pressure. The mixed wear-resistant material powder is heated at 200-500 degrees, and the pressure is repeated four times, each time the pressure is 6MPa, 15MPa, 10MPa, 20MPa.
PUM
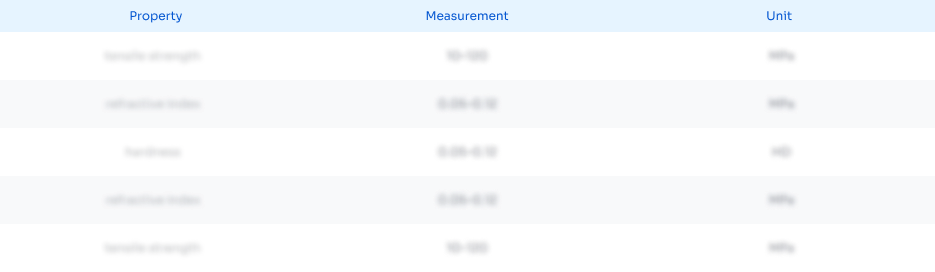
Abstract
Description
Claims
Application Information

- R&D Engineer
- R&D Manager
- IP Professional
- Industry Leading Data Capabilities
- Powerful AI technology
- Patent DNA Extraction
Browse by: Latest US Patents, China's latest patents, Technical Efficacy Thesaurus, Application Domain, Technology Topic, Popular Technical Reports.
© 2024 PatSnap. All rights reserved.Legal|Privacy policy|Modern Slavery Act Transparency Statement|Sitemap|About US| Contact US: help@patsnap.com