A compressor system for a rail vehicle and method for operating the compressor system with safe emergency operation
A technology for compressor systems and rail vehicles, which can be used in machine/engine, railway signal and safety, railway vehicle heating/cooling, etc., and can solve problems such as rail vehicle stop
- Summary
- Abstract
- Description
- Claims
- Application Information
AI Technical Summary
Problems solved by technology
Method used
Image
Examples
Embodiment Construction
[0022] according to figure 1 , a compressor system for a rail vehicle has an electric motor 1 , which drives a compressor 3 for generating compressed air via a drive shaft 2 . The compressed air produced by the compressor 3 is conducted via a compressed air-conducting line 6 to a cooling unit 9 with a cooling fan 14 . Downstream of the cooling unit 9 , a pressure sensor 7 and a temperature sensor 13 b are arranged in the line 6 carrying compressed air. Furthermore, the line 6 carrying compressed air leads into a pre-separator 11 , after which an air treatment unit 12 is connected. Dry and particle-free compressed air is then fed into the compressed air container 4 . Furthermore, a pressure switch 16 for monitoring the pressure in the compressed air container 4 and for indirectly influencing the speed of the electric machine 1 and the cooling fan 14 is arranged in the line 6 carrying the compressed air.
[0023] The temperature sensor 13 a , the temperature sensor 13 b and t...
PUM
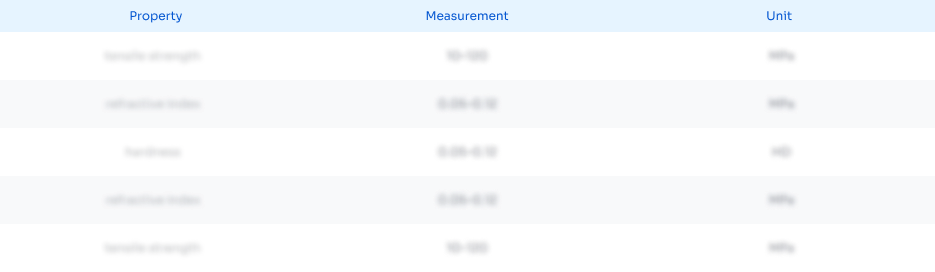
Abstract
Description
Claims
Application Information

- R&D Engineer
- R&D Manager
- IP Professional
- Industry Leading Data Capabilities
- Powerful AI technology
- Patent DNA Extraction
Browse by: Latest US Patents, China's latest patents, Technical Efficacy Thesaurus, Application Domain, Technology Topic, Popular Technical Reports.
© 2024 PatSnap. All rights reserved.Legal|Privacy policy|Modern Slavery Act Transparency Statement|Sitemap|About US| Contact US: help@patsnap.com