Spiral filler strip type winding pipe heat exchanger
A wound tube type and spiral type technology, which is applied in the field of spiral pad type wound tube heat exchangers to achieve the effects of enhanced heat transfer performance, enhanced heat transfer, and increased tangential velocity
- Summary
- Abstract
- Description
- Claims
- Application Information
AI Technical Summary
Problems solved by technology
Method used
Image
Examples
Embodiment Construction
[0022] The present invention will be described in detail below in conjunction with the accompanying drawings.
[0023] refer to figure 1 and figure 2 , a spiral gasket type wound tube heat exchanger, including the i-th layer of heat exchange tubes 1 and the i-1th layer of heat exchange tubes 2, the i-th layer of heat exchange tubes 1 and the i-1th layer of heat exchange tubes 2 The i-th layer of spiral flat gasket 3 and the i-th layer of spiral special-shaped gasket 4 are arranged between them, and the i-th layer of spiral flat gasket 3 controls the layer spacing P between different layers of heat exchange tubes l , the i-th layer of spiral special-shaped gasket 4 controls the tube spacing P between the heat exchange tubes of the same layer t , the i-th layer of spiral-shaped flat pads 3, the i-th layer of spiral-shaped special-shaped pads 4 make the flow channel formed between the heat exchange tube layers perpendicular to the heat exchange tubes of this layer, and the i-t...
PUM
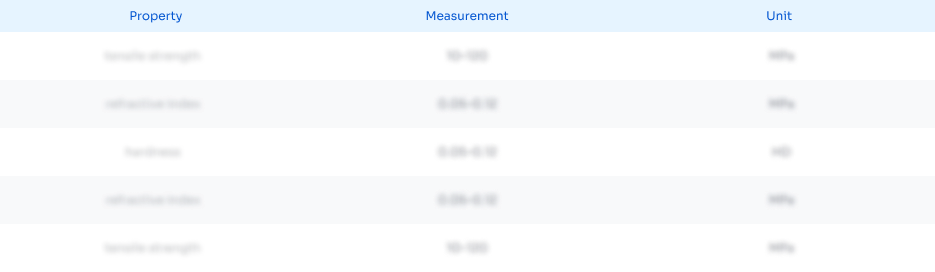
Abstract
Description
Claims
Application Information

- R&D
- Intellectual Property
- Life Sciences
- Materials
- Tech Scout
- Unparalleled Data Quality
- Higher Quality Content
- 60% Fewer Hallucinations
Browse by: Latest US Patents, China's latest patents, Technical Efficacy Thesaurus, Application Domain, Technology Topic, Popular Technical Reports.
© 2025 PatSnap. All rights reserved.Legal|Privacy policy|Modern Slavery Act Transparency Statement|Sitemap|About US| Contact US: help@patsnap.com